آشنایی با مشخصات شمش ، بیلت ، بلوم و اسلب
آشنایی با مشخصات شمش ، بیلت ، بلوم و اسلب و تفاوت آن ها
در بیان عامیانه باید بگوییم که بیلت ، بلوم و اسلب همه از شمش ساخته می شوند اما تفاوت های زیادی با هم دارند. این محصولات از کالاهای فولادی نیمه ساخته هستند که برای تبدیل شدن به محصول نهایی باید فرآوری شوند.
در این مقاله ما قصد داریم با انواع شمش و مشخصات آن ها و همینطور تفاوت آن با بیلت ، بلوم و اسلب آشنا شویم. شمش فولادی اصلی ترین مواد اولیه برای تولید انواع مقاطع فولادی از جمله میلگرد ، تیرآهن ، بلوم ، اسلب ، بیلت و غیره است. محصولاتی مانند اسلب ، بیلت ، بلوم ، کالاهای نیمه فولادی است که برای تبدیل به محصولات نهایی مورد استفاده قرار می گیرد.
شمش چیست؟ ( Ingot )
شمش قالب هایی کوچک از مواد فلزی است که با ذوب انواع فلزات مانند طلا، فولاد، قلع، آلومینیوم ( مشخصات فلز آلومینیوم ) ، تلوریم، برنج ( خواص و کاربرد برنج )، مس ( کاربردهای فلز مس در صنعت ) و استیل ( مشخصات و کاربرد استیل ) و … تولید می شود. شکل سطح مقطع عرضی شمش ذوزنقه بوده که طولی کمتر از دو متر دارد. شمش فولادی از جمله فرآورده های میانی نورد فولاد است. شمش فولادی به دو صورت بیلت ( Billet ) و بلوم ( Bloom ) تولید می گردد.
در واقع شمش ها محصولات نیم ساخته مسی هستند که باید طی مراحل و فرایندهای گوناگون به محصول مورد نظر تبدیل شوند. در نورد فولاد به فراورده هایی با سطح مقطع بزرگتر از ۲۲۵ سانتیمتر شمش مس و به فراورده هایی با سطح مقطع کوچکتر از آن شمشال ( بیلت ) گفته می شود و از این رو بیشتر برای مصارف تولید میلگرد و سیم استفاده می شود.
شمش فولادی که به صورت بلوم تولید می گردد، تحت عنوان شمشه نیز شناخته می شود. بلوم نیز دارای سطح مقطعی کمتر ۲۳۰ سانتی متر مربع است اما عرض آن بیش از ۱۵ سانتی مترمربع است. شمش فولادی بلوم معمولا برای مصارف ساخت ریل قطار، سپری، ناودانی، قوطی، تیرآهن کاربرد دارد.
در صنایع بزرگ فولادی عموماً واژه شمش فولادی به انواع بلوم ، بیلت یا اسلب اطلاق میگردد. همچنین شمشها دارای گریدهای مختلفی از جمله ۳SP – 5SP ( استاندارد روسی ) و St37 – St52 ( استاندارد DIN آلمان ) است که با وجود درصدهای مختلف از عناصر گوناگون موجود در فولاد دارای خواص مکانیکی متفاوت مثل انعطافپذیری ، خمش ، کشش و پیچش بوده و کاربردهای متنوعی را میطلبد.
کاربردهای شمش
شمش کاربردهای مختلفی در بخش های گوناگون دارد. بسته به مواد و اندازه در صنعت ساخت و ساز و ماشین آلات نقش مهمی دارد. شمش های تولید شده با ریخته گری می توانند ۳۰۰ کیلو تا ۹ تن وزن داشته باشند از این رو در صنایع سنگین مانند: کشتی سازی و جرثقیل های سنگین استفاده می شود. شمش فولاد برای مصارفی استفاده می شوند که نیاز به ذوب و قالب گیری باشد یعنی به صورتی که محصول نهایی تنها از راه ریخته گری ایجاد می شود. مانند قطعات سنگین و اشکال خاص.
تولید شمش در ایران دومین صنعت مهم و استراتژیک محسوب می شود. آسیا بزرگترین کارخانه های تولید شمش فولاد در دنیا را در خود جای داده است, که چین در این حوزه جزو صنعت مادر شناخته می شود و ۴۲ درصد فولاد دنیا را تولید می کند.
تولید شمش فولادی
شمش فولاد مواد اولیه تولید فرآورده های فولادی است. فولاد روش های مختلفی از جمله های کوره بلند (BF)، کوره قوس الکتریکی (EAF) و کوره القایی (IMF) برای تولید فولاد خام یا مذاب وجود دارد. برای تولید شمش فولاد از روش EAF یعنی کوره قوس الکتریکی استفاده می شود.
تولید شمش فولاد به روش قوس الکتریکی ابتدا آهن قراضه داخل این کوره ریخته می شود سپس مخلوطی از آهن اسفنجی (Sponge Iron ، آهک، کک، بنتونیت و مواد افزودنی دیگر) به آن اضافه می شود و سپس نمونه گیری انجام می شود و در آن اکسیژن دمیده می شود تا به فولاد مذاب تبدیل می گردد. مخلوط مذاب تولید شده پس از تخلیه سرباره به واحد ریخته گری ارسال می شوند. سپس مواد مذاب داخل ظروف تانديش ریخته شده و بعد از آن داخل قالب مسی آبگرد و سپس در طول مسیر غلطکی با پاشش آب خنک، به شمش منجمد تبدیل می گردد.
روش کوره بلند ( BF )
بیش از ۹۰ درصد از سنگ آهنی که در جهان استخراج میشود در کورههای بلند مورد استفاده قرار میگیرند. در این روش سنگ آهن پس از اینکه پیش پخت و کلوخه سازی گردید، به همراه کک و آهک داخل کوره بلند ریخته شده و آهن خام یا چدن به دست میآید.
سپس آهن خام در کانورتر به فولاد مذاب تبدیل میشود. در مرحله بعد، ناخالصیهای فولاد خام مانند کربن را بهوسیله اکسیژن از آن جدا می کنند تا فولاد خام به دست آید. فولاد مذاب پس از جداسازی ناخالصی توسط پاتیل های حمل مذاب به واحد ریخته گری برده میشود.
سپس مواد مذاب را در واحد ریخته گری داخل قالب های شمش ریخته و بر روی غلتکی قرار داده و با پاشیدن آب به خنک کردن آن اقدام می نمایند. پس از خنک شدن، شمش فولادی را به طول دلخواه برش میدهند.
کوره های قوس الکتریکی ( EAF ) و کوره القایی ( IMF )
آهن قراضه را با سبدهای مخصوص در کوره قوس الکتریکی می ریزند و بعد از آن آهن اسفنجی را با مواد سرباره سازی مانند کک، آهک، بنتونیت، و… از بالا به کوره اضافه می گردد. پس از افزودن این مواد اقدام به نمونه گیری، دمش اکسیژن، همگن سازی و آنالیز کرده تا مواد داخل کوره به فولاد مذاب تبدیل شود.
فولاد مذاب پس از جداسازی ناخالصی توسط پاتیل های حمل مذاب به واحد ریخته گری برده می شود. در ریخته گری مواد مذاب را داخل ظروفی به نام تاندیش می ریزند و بعد آن را داخل قالب مسی آب گرد و بر روی غلتکی قرار داده و با پاشیدن آب به خنک کردن آن اقدام می نمایند. در ادامه شمشهای منجمد به دست آمده را به طول های مورد نظر برش می دهند.
مرحله کوره الکتریکی ، فرآیند ذوب شدن ذوب فلزات فلزی است. یک کوره الکتریکی از الکتریسیته برای حرارت دادن قراضه فولاد استفاده می کند. بسته به روش های گرمایش، آن را به کورههای قوس و کوره های مبتنی بر DC ( جریان مستقیم ) تقسیم می شود، این یک فرایند ساخت فولاد تصفیه شده پودر به بیلت است.
در طول ریخته گری پیوسته، فولاد تاکنون مایع باقی مانده است، به یک شکل ثابت می شود. شمش نیمه خام برای تولید طیف گسترده ای از محصولات پس از فرآیندهای مختلف استفاده می شود. بیلت ساخته شده در فرآیند ریخته گری مداوم به آسیاب از طریق یک سیستم انتقال خودکار تغذیه می شود.
ویژگی های شمش فولادی
شمش فولادی دارای ۲ گرید ۳SP و ۵SP از استاندارد فولاد ST37 می باشند. ۳SP و ۵SP در دسته فولادهای ساده کربنی قرار می گیرند که قابلیت عملیات حرارتی ندارند. از این رو کاربردهای آن، در مواردی است که استحکام بالا مورد انتظار نباشد. ۳SP انعطاف بیشتری دارد و در صنایع نیازمند خمش و کشش استفاده می شود. شمش ۵SP انعطاف پذیری کمتری دارد و در صنایع با ثبات استفاده می شود که تحت نیرو و فشار نباشند.
مراحل تولید شمش فولاد
در ابتدا بهتر است بدانیم که سنگ آهن ماده اولیه تولید فولاد است. برای تولید فولاد باید فرآیند طولانی و سختی را از سر گذراند. بیشتر سنگ آهنی که در جهان استخراج می شود در کوره های بلندی مورد استفاده قرار می گیرند. در این کوره ها و طی فرآیندی، پس از مرحله پیش پخت و کلوخه سازی، کک و آهک را به کوره اضافه میکنند تا آهن و چدن را از سنگ آهن جدا کنند.
بعد از آن، آهن خام به فولاد مذاب تبدیل می شود. سپس ناخالصی های فولاد خام مانند کربن به وسیله اکسیژن را از آن جدا میکنند تا فولاد خام به دست آید. فولاد مذاب پس از جداسازی ناخالصی به واحد ریخته گری برده می شود تا مواد مذاب را در واحد ریخته گری داخل قالب ها ریخته و بر روی غلطکی قرار داده و با پاشیدن آب به خنک کردن آن اقدام میکنند.
پس از خنک شدن شمش فولادی را به طول دلخواه برش می دهند. روش کوره الکتریکی و کوره القایی هم از دیگر روش های تبدیل سنگ آهن به فولاد است. بیشتر فولاد جهان به روش کوره بلند تهیه می شود اما در ایران از روش کوره الکتریکی استفاده می شود.
-
روش کوره الکتریکی
در این روش ابتدا آهن قراضه را با کمک سبدهای مخصوص، داخل کوره می ریزند و هم زمان با ذوب قراضه ها، ترکیبی از آهن اسفنجی و مواد سرباره ساز مثل کک، بنتونیت، آهک، سایر مواد افزودنی از قسمت بالای کوره به ذوب افزوده می شود و بعد از نمونه گیری، دمش اکسیژن ( که باعث اکسیداسیون ناخالصیها به ویژه کربن در مذاب می شود ) صورت می گیرد و بعد از آن همگن سازی و … است که به فولاد مذاب تبدیل می شود.
در واحد ريخته گری، ظروفی به نام تاندیش مذاب را به داخل قالب مسی آب گرد ریخته و سپس در طول مسیر غلطکی با پاشش آب خنک به شمش فولادی منجمد تبدیل می کند.
در نهایت تختال های تولید شده به طول های مورد نظر برش داده می شوند. آهن اسفنجی، که در تولید شمش فولادی مورد استفاده قرار میگیرد از طریق احیای مستقیم گندله تولید می شود. شمش سطحی ذوزقه ای شکل است که طول هر شاخه آن حداکثر ۲ متر است و تفاوت در شکل مقطع و ابعاد آن، نوع هایی را به وجود میآورد. ظرفیت کوره های قوس الکتریکی از یک کیلوگرم تا بیست تن متغییر است. به طور مثال فولاد کویر کاشان از روش قوس الکتریکی استفاده میکند که تفاوت قیمتی و کیفیتی زیادی با محصولات شمش کوره القایی دارد.
قیمت شمش فولادی
قیمت شمش فولادی به عوامل مختلفی از جمله برند کارخانه سازنده، مواد اولیه مرغوب به کار رفته و قیمت شمش فولاد در بازار جهانی بستگی دارد. قیمت شمش فولادی متأثر از نرخ دلار نیز می باشد و با توجه نوسانات اخیر ارزی شاهد بی ثبات بودن قیمت آن در بازار شمش بوده ایم.
چرا کربن در شمش مهم است؟
اهمیت کربن موجود در شمش از جایگاه ویژه ای برخوردار است. چرا که برای تولید میلگرد از شمش فولادی استفاده می شود و میزان کربن موجود در شمش ها برای تولید میلگرد مهم است. اگر بخواهیم میلگرد سایز ۱۴ تا ۴۰ تهیه کنیم، شمش باید با کربن ۳۰ تا ۳۵ باشد و برای سایزهای پایین تر، نیاز به کربن کمتری است. چرا که در سایزهای پایین تر کشش و نرمی بیشتری نیاز است.
شمش ۱۲۵، ۱۳۰ و۱۵۰ برای تولید میلگرد مناسب است و در کارخانه های مدرن و به روز امکان تولید میلگرد با هر دو شمش وجود دارد. شمش با ابعاد ۱۰۰ ، ۱۲۰ ، ۱۲۵ ، ۱۳۰ ، ۱۵۰ ،۱۶۰ را بیلت و شمش با ابعاد ۱۸۰ * ۱۸۰ ، ۲۰۰ * ۲۰۰ ، ۲۵۰ * ۲۵۰ را بلوم گفته و برای تولید میلگردهای صنعتی مصرف می شود.
بیلت یا CCM ( Billet )
اصطلاح علمی تر که در سراسر دنیا به این نام می شناسند CCM است. اگر شمش به طور مستقیم از توليد ccm به مصرف نورد برسد به آن شمش ccm يا بيلت گفته مى شود. بیلت را به عنوان شمشال نیز می شناسند، طول بیشتری نسبت به شمش دارد و سطحی دایره شکل یا مربعی با عرضی کمتر از ۱۵ سانتی متر دارد و به عبارتی سطح مقطع آن کوچک تر از ۲۳۰ سانتی متر مربع است. بیلت ها در اثر ریخته گری شمش مس حاصل می شود.
از بیلت در ساخت تمام مقاطع فولادی به جز ورق استفاده می شود. رایج ترین محصول تولید شده از بیلت میلگرد و سیم است که در پروژه های عمرانی و ساختمانی کاربرد زیادی دارد. بیلت در پل سازی و صنایع ریلی و اکستروژن هم کاربرد دارد. میلگرد، سیم مسی، تیرآهن، مفتول، میلگرد ساده و آجدار، نبشی، ناودانی، سپری، لوله های بدون درز و مانیسمان از دیگر مواردی هستند که در ساخت آن ها از بیلت استفاده می شود.
بيلت در رده های مختلفی مانند ۳sp و ۵sp توليد می شود. بيلتی که انعطاف پذیر است و نسبت به کشش، خمش و پیچش انعطاف پذیرتر باشد، بیلت ۳sp است. بلیت ۵sp انعطاف پذیر نیست و برای مواقعی که سازه در معرض نيرو و فشار نيست، استفاده می شود و تقريبا با ثبات است. قیمت بیلت ۳sp بیشتر است. از گرید ۵sp معمولاً در ساخت میلگرد استفاده می گردد و از گرید۳sp در نورد مقاطعی مانند تیرآهن و نبشی استفاده میشود.
فرآیند تولید بیلت از فرآوردههای میانی نورد
بیلت را به دو روش یکی از طریق «خروجی کوره بلد» و دیگری از طریق «خروجی کورههای قوس الکتریک» تهیه میکنند، که در ادامه به بررسی این دو روش میپردازیم.
قیمت داخلی و جهانی بیلت
قیمت بیلت در بازار ایران، با توجه به عرضه و تقاضای موجود در بورس کالای کشور تعیین می گردد. با توجه به اینکه میزان ۸۵ درصد کالاهای نوردی بازار فولاد ایران به مصرف داخل می رسد، نوسانات بازارهای بینالمللی بر این کالا اثر مستقیم نمیگذارد و قیمت شمش فولادی در ایران به نسبت قیمت بین المللی آن عمدتاً پایین تر است.
برای قیمت مبادله شده بیلت ترکیه: ۴۶۰-۴۵۰ $/ton در هر تن و برای بیلت CIS : ۴۶۰-۴۵۰ $/ton به ثبت رسیده است. با توجه به قیمت ارز همچنان نگاه تولیدکنندگان به صادرات است که می تواند در ارز آوری کمک شایانی به اقتصاد کشور داشته باشد.
معروف ترین تولیدکنندگان بیلت در ایران
-
ذوب آهن اصفهان
مادر صنعت فولاد ایران، ذوب آهن اصفهان است که اولین و بزرگ ترین تولیدکننده فولاد ساختمانی در کشور است. این کارخانه در جنوب غربی استان اصفهان و در نزدیکی شهرستان زرین شهر احداث شده است. محصولات کارخانه ذوب آهن اصفهان به بیش از ۲۳ کشور آسیایی، آفریقایی و اروپایی صادر می شود. عمده ترین محصولات این کارخانه تیرآهن I شکل و H شکل، میلگردهای ساده و آجدار، نبشی، ناودانی و بیلت است.
-
فولاد مبارکه اصفهان
این کارخانه اولین کوره قوس الکتریکی خود را راه اندازی نمود. ظرفیت تولید این مجتمع به قدری است که بخش قابل توجهی از نیازهای کشور را تحت پوشش قرار می دهد. فولاد مبارکه اصفهان در ۷۵ کیلومتری جنوب غربی شهر اصفهان واقع شده است.
محصولات این واحد بزرگ صنعتی شامل بیلت ، اسلب ، لوله های نفت و گاز ، ورق آجدار ، ورق قلع اندود ، ورق رنگی ، ورق گالوانیزه و … است. در حال حاضر این کارخانه یکی از بزرگ ترین واحد های صنعتی در کشور است که علاوه بر تامین نیازهای داخلی، میزان قابل توجهی از تولیدات خود را نیز صادر می کند.
-
فولاد خوزستان
فولاد خوزستان روش کوره بلند و کوره قوس الکتریکی را برای اولین بار در کشور به کار گرفت. این واحد بزرگ صنعتی در استان خوزستان و در نزدیکی شهر اهواز واقع شده است. ظرفیت تولید سالانه فولاد خوزستان در حدود ۳.۸ میلیون تن است. این مجتمع به عنوان بزرگ ترین عرضه کننده بیلت و دومین قطب تولید فولاد خام در ایران شناخته شده است. محصولات این شرکت شامل بیلت ، اسلب ، بلوم ، گندله و … است.
علاوه بر ذوب آهن و فولاد مبارکه اصفهان، تولیدکنندگان دیگری نیز در تولید بیلت پیشرو هستند که در ادامه نام تعدادی از این کارخانه ها را مشاهده می کنید.
- مجتمع فولاد کیمیا
- فولاد آتیه اندیشان سپهر شرق
- فولاد خزر
- فولاد شاهین بناب
- فولاد آلیاژی ایران
- فولاد ارفع
- فولاد پاسارگاد
- فولاد کاوه جنوب
- فولاد کاویان
- فولاد سیرجان
- نورد فولاد یزد
- فولاد هرمزگان
- فولاد جم قم
- فولاد سازان کیوان یزد
- ویان همدان
عوامل موثر بر قیمت بیلت چیست
مانند هر محصول دیگری، عوامل متعددی بر قیمت شمش آهن و بیلت تاثیرگذار است که در این قسمت میخواهیم به بررسی این عوامل بپردازیم.
-
قیمت سنگ آهن
همان طور که قبل تر هم اشاره شد، یکی از مواد اولیه مورد نیاز برای تولید انواع بیلت، سنگ آهن است. بنابراین کاملا طبیعی به نظر می رسد که قیمت بیلت صادراتی و داخلی متاثر از قیمت سنگ آهن باشد.
-
قیمت جهانی نفت
حدود ۱۵ درصد از قیمت بیلت و به طور کلی محصولات فولادی ناشی از میزان انرژی مصرف شده برای تولید آن ها است. بنابراین با افزایش قیمت جهانی نفت، شاهد افزایش قیمت تمام شده بیلت و محصولات فولادی خواهیم بود.
-
قیمت ضایعات آهن
با توجه به این که در تولید بیلت از ضایعات آهن نیز استفاده می شود، از این رو قیمت ضایعات بر قیمت نهایی بیلت تاثیرگذار خواهد بود. تولید ضایعات در ایران محدود است. لذا می توان آهن اسفنجی را جایگزین ضایعات آهن کرد.
-
عرضه و تقاضا
به طور کلی عرضه و تقاضا نقش کلیدی در تعیین قیمت نهایی یک محصول دارد. به این صورت که با افزایش عرضه قیمت کاهش و با افزایش تقاضا قیمت افزایش پیدا می کند.
-
هزینه حمل و نقل
یکی از فاکتورهای موثر بر قیمت بیلت، هزینه حمل و نقل آن است.
-
تولیدکنندگان عمده جهانی
سیاست های تولیدکنندگان جهانی بیلت، می تواند روی قیمت آن تاثیر زیادی داشته باشد. به عنوان مثال کاهش میزان صادرات، می تواند موجب افزایش قیمت بیلت صادراتی شود.
-
نرخ ارز
به طور کلی با افزایش نرخ ارز، تقاضا برای آهن آلات و همچنین بیلت کاهش پیدا می کند. بنابراین نوسانات ارزی و به تبع آن تغییر میزان تقاضا بر قیمت بیلت تاثیر می گذارد.
بلوم یا فابریک ( Bloom )
در صورتی که سطح مقطع بیلت عریض تر باشد، بلوم نامیده می شود. بلوم را با نام شمسه نیز می شناسند. بلوم در واقع همان بیلت است که سایز متفاوتی دارد. یعنی عرض اش بیش از ۱۵ سانتی متر است، به عبارتی می توان گفت سطح مقطع کوچک تر از ۲۳۰ سانتی متر و مربعی است و به همین دلیل معمولا بلوم و بیلت در یک دسته قرار می گیرند.
بیشترین مصرف بلوم برای ساخت ریل، سپری، ناودانی، قوطی و … است. در گذشته نام بلوم بیشتر استفاده می شد اما به مرور زمان، تجار این صنف نام فابریک را بر این محصول گذاشتند، هر چند که هنوز قدیمی های این بازار این محصول را بلوم هم می گویند.
مراحل تولید بلوم
داخل محفظه هایی مستطیل شکل با عمق ۵ متر که در آن ۴ تا ۶ قالب بلوم آهن به طور همزمان در دمای ۱۲۵۰ درجه سانتی گراد گرم می شوند. برای گرم شدن به ۸ تا ۱۸ ساعت لازم دارد .
پس از گرم شدن شمش آهن قابل انعطاف می شود و به یک آسیاب معکوس دو طبقه انتقال می یابد که با هر بار عبور از این آسیاب از بین رول ها و غلتک های معکوس عبور کرده از آنجا که با هر بار عبور فقط ۵۰ سانتیمتر از ضخامت آن کاهش می یابد ممکن است که ۲۱ مرتبه لازم باشد تا از بین غلتک ها عبور کند تا به ضخامت مورد نظر برسند.
با عبور از چندین ایستگاه بلوم به ضخامت ۲۰ سانتی متر و عرض ۱۵ سانتی و طول ۱۰ متر در می آید وزن بلوم حدودا که قطر غلتک ها حدود ۱۲۰ سانتی متر است و هر یک توسط یک یا دو موتور الکتریکی در مجموع ۷۰۰۰ تا ۱۲۰۰۰ اسب بخار هدایت می شوند. دو میز غلتکی که در جلو و عقب جایگاه قرار دارد بازوهای متحرکی دارند که بلوم آهن را به داخل هدایت می کند و در صورت لزوم لبه های آن را می چرخاند.
عوامل موثر در مقاومت شمش بلوم
عوامل زیادی در مقاومت و استحکام فولاد نهایی که به شکل شمش بلوم یا سایر انواع شمش از ذوب آهن خارج میشود، تاثیر گذار هستند. این که این شمشها از سنگ آهن ساخته شده باشند یا آهن آلات ضایعاتی را مجددا بازیافت کنند هم میتواند در مقاومت آنها تاثیر گذار باشد. اما به طور کلی وجود یک ماده خاص در فولاد می تواند مقاومت آن را تا حد زیادی کنترل کند و آن ماده کربن است. برای تولید شمش های مختلف باید میزان کربن موجود در آن کنترل شود.
برای مثال در تولید میلگرد، به طور معمول از شمشهایی که دارای کربن کم تری هستند، برای ساخت میلگردهایی با ضخامت کمتر استفاده می شود. این میلگردها معمولا قابلیت انعطاف بیشتری هم دارند. به همین ترتیب، شمش هایی که دارای کربن بیشتری هستند، برای تولید میلگردهای با ضخامت بیشتر مورد استفاده قرار می گیرند. بنابراین، کربن یکی از مهم ترین عوامل تعیین کننده مقاومت و استحکام شمش Bloom است.
فولاد کم آلیاژ پر استحکام دسته ای جداگانه از فولادهای ساده کربنی هستند که مقدار عناصر آلیاژی در آن ها بسیار کم است اما حضور همین عناصر سبب بهبود خواص مکانیکی می شود.
اسلب ( Slab )
اسلب همان بلوم است با این تفاوت که سطح مقطع آن مستطیلی است. قطعه ای مکعب مستطیل از فولاد است که بر خلاف بیلت و بلوم است. اسلب یک محصول میان خطی و نیمه نهایی فولاد است که از فرایند نورد شمش و یا فرایند ریخته گری پیوسته حاصل می شود. سطح مقطع اسلب ها بر خلاف شمشه و شمشال مربعی نیست بلکه مستطیلی بوده و به عنوان ماده اولیه برای ساخت محصولات نورد تخت از جمله کویل و ورق نورد گرم، استفاده می شود.
به اسلب، تختال نیز می گویند. اسلب مواد اولیه ساخت ورق فولادی است. این نکته مهم است که بلوم از كنار اسلب بريده می شود.
نکته اول که باید به آن توجه کنید این موضوع است که سطح اسلب فولاد بر خلاف بیلت و بلوم مربع نبوده و مستطیل شکل است. عرض آن ۱٫۲۵ متر، طول آن ۱۲ متر و ضخامت آن ۲۳۰ میلیمتر در نظر گرفته می شود. اسلب برای ساخت ورق های فولادی، صفحه و … به کار می رود.
اغلب اسلب ها از جنس فولاد کربنی است اما اسلب های از جنس فولاد زنگ نزن نیز یافت می شود. این محصول از آلیاژهایی مثل آهن، کروم، مس، منگنز، نیکل، سیلیسیوم، نیکل و مولبیدن تشکیل میشود. مشخصات مربوط به آن از طریق کدهای استاندارد که معمولا در قسمت انتهایی اسلب حک شده است، مشخص می شود.
برخی از استانداردهای اسلب عبارت اند از :
وضعیت تولید فولاد خام و فرآوردههای میانی نورد فولاد در ایران در شرایط مناسبی به سر می برد و در حال حاضر ایران جزو ده تولیدکننده برتر فولاد در جهان است.
کاربردهای اسلب
بیلت، بلوم و اسلب نام تجاری ۲۲ محصول فولادی می باشد که آنها را در ساخت انواع مختلف مقاطع و محصولات فولادی مورد استفاده قرار می دهند. از اسلب برای تولید انواع محصولات تخت فولادی مثل ورق، صفحات و کویل و همچنین در صنعت ماشین آلات سنگین استفاده میشود. با توجه به ابعاد استاندارد اعلام شده، ضخامت این ورق فولادی بسیار کم است. به طوری که ممکن است باعث بروز مشکل هنگام برش شود و نیاز باشد برای برش از دستگاه هایی با امکانات بالا استفاده کرد.
روش های تولید اسلب
گرچه برای تولید محصولات فولادی فناوری های مورد استفاده بعد از به دست آوردن فولاد مذاب تقریباً یکسان است، با این حال سه روش عمده برای تولید اسلب مطرح است که در زیر لیست شدهاند :
الف ) روش کوره بلند، کنور تور ( روش سنتی )
روش کوره بلند یک روش سنتی است که از احیا غیرمستقیم برای تولید اسلب استفاده می شود. با توجه به اینکه ایران دارای منابع زغال سنگ مرغوب است این روش یک روش کاربردی است. در ابتدا سنگ آهن همراه با آهک و کک را وارد کوره بلند می کنند و آهن خام ( چدن مذاب ) استخراج می شود. برای از بین بردن ناخالصی های فولاد مذاب به دست آمده از آهن خام، با حذف کربن و اضافه کردن اکسیژن فولاد خام به دست می آید.
در ادامه در واحد ریخته گری مداوم، مذاب به داخل قالب ریخته می شود با جدا کردن محصول از قالب و عملیات پاشش آب خنک تختال خنک شده و به شمش منجمد تبدیل می شود. در انتها با برش های مختلف می توان به طول های موردنظر اسلب دست یافت.
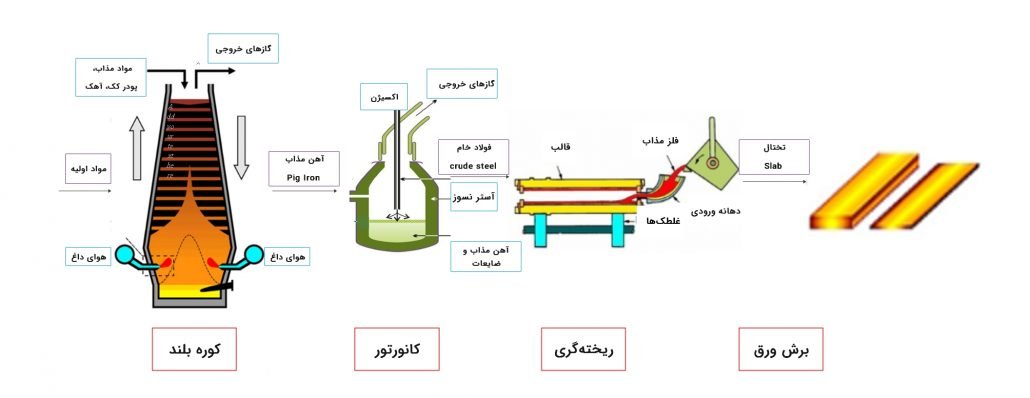
ب ) کوره الکتریکی
روش دو تولید فولاد، استفاده از کوره های الکتریکی و ذوب مجدد قراضه آهن و فولاد هست، در این روش سبدهای آهن در داخل کوره ریخته می شود. به دلیل کمبود منابع قراضه در جهان و نیز رشد فزاینده قیمت آن در طول سال های گذشته، در این روش به همراه قراضه از آهن اسفنجی نیز برای ذوب در کوره استفاده میشود.
بنابراین هم زمان با ذوب آهن قراضه ها، ترکیبی از آهن اسفنجی و مواد سرباره ساز مثل کک، بنتونیت، آهک و سایر مواد افزودنی از قسمت بالای کوره به ذوب افزوده می شود و بعد از نمونه گیری، با اضافه کردن اکسیژن، ناخالصی ها به ویژه کربن در مذاب اکسید می شوند. در نهایت با همگن سازی فولاد مذاب تولید می شود. در واحد ریخته گری، فولاد مذاب به داخل قالب مسی آبگرد ریخته و سپس با پاشش آب خنک به شمش فولادی منجمد تبدیل می شوند.
ج ) کوره القایی
روش کوره القایی به دلیل استفاده از برق، الکترود و مواد افزودنی هزینه بالایی را به همراه خود دارد، از طرف دیگر در این کوره ها دو مشکل وجود دارد که باعث شده است در فولادسازی ایران مورد استفاده قرار نگیرند.
مشکل اول : این است که کوره القایی به خوبی نمی تواند اکسیژن را کنترل کند و همین امر باعث عیوبی در محصول می شود، چراکه به دلیل قلیان اکسیژن محلول در مذاب اکسید شدن فرو آلیاژ پیش می آید.
مشکل دوم : این روش، فسفر زدایی و گوگرد زدایی کوره القایی است.
با وجود اینکه در جهان از روش کوره بلند برای تولید فولاد خام و اسلب استفاده می کنند اما به دلایل متعددی استفاده از روش کوره الکتریکی در ایران توجیه پذیر است که کورههای قوس الکتریکی فولاد خوزستان از جمله کوره های با ارزش در زمینه تولید اسلب است.
کارخانه های تولید اسلب در ایران
با توجه به اینکه اسلب در بین محصولات فولادی جایگاه ویژه ای کسب کرده است در کارخانه های ذوب آهن اصفهان، فولاد خوزستان ، فولاد هرمزگان ، فولاد مبارکه اصفهان و چادرملو تولید می شود که کارخانه فولاد هرمزگان در خصوص تولید اسلب شناخته شده است؛ اسلب تولیدی در این کارخانه ها ضخامتی بین ۱۸۰ تا ۳۰۰ میلی متر دارد و طول آن ۴، ۶، ۱۰ و ۱۲ است.
با توجه به اینکه از چند سال اخیر تاکنون تولید این محصول با رعایت استانداردهای جهانی تولید می شود به کشورهای مختلف آسیایی و حتی اروپایی صادر می کند.
تفاوت انواع شمش ، بیلت ، بلوم و اسلب چیست
شمش، بیلت، بلوم و اسلب، کالاهای فولادی نیمه ساخته ( فرآوردههای میانی نورد فولاد ) محسوب می شوند که برای تبدیل شدن به محصول نهایی بایستی یک یا چند مرحلهی دیگر فرآوری شوند. تفاوت این محصولات در ابعاد و شکل سطح مقطع آن هاست که در ادامه این چهار محصول را بررسی خواهیم کرد.
- شمش : طول این محصول کمتر از ۲ متر است و ابعاد آن برای حمل و نقل فولاد و انبار کردن آن بهینه شده است. شکل سطح مقطع عرضی آن ذوزنقه شکل است.
- سطح مقطع بیلت دایره یا مربع و بعضا هشت ضلعی است. در حالی که سطح مقطع اسلب مستطیل شکل است.
- بیلت برخلاف شمش طول بیشتری دارد و به همین دلیل هم در ساخت محصولات طویل فولادی مانند میلگرد و مفتول، از بیلت استفاده می شود.
- بیلت از طریق ریختهگری مستقیم، اکستروژن (بیرون رانی) و یا از طریق نورد شمش به دست میآید.
- بیلت سطح مقطع کوچکتری نسبت به بلوم دارد.
- اگر عرض بیلت ( شمشال ) بیش از ۱۵سانتیمتر (یا سطح مقطع بیش از ۲۳۰سانتیمتر مربع ) باشد آن را بلوم می نامند و به همین دلیل معمولاً این دو کالا را در یک دسته ( بلوم و بیلت ) جای می دهند. از بلوم برای ساخت ریل، تیر آهن، قوطی، ناودانی، سپری و … استفاده میشود.
- سطح مقطع اسلب بر خلاف بلوم و بیلت مربعی نیست بلکه مستطیلی است (معمولاً به ضخامت ۲۳۰ میلیمتر و عرض ۱٫۲۵ متر و طول ۱۲ ) . از اسلب برای ساخت ورقهای فولادی، صفحه و … استفاده میشود.
- اسلب عموما در ساخت ورق و کویل و بلوم در ساخت تیرآهن و ناودانی کاربرد دارد. اما از بیلت در ساخت میله، انواع میلگرد و مفتول استفاده می شود.
- بیلت چگالی بیشتری نسبت به انواع دیگر شمش دارد.
- کاربرد بیلت ها در صنعت بیشتر از انواع دیگر شمش است.
دیدگاهتان را بنویسید