روشهای شکلدهی فلز
شکلدهی فلز یک اصطلاح کلی است که به طیف گستردهای از فرایندهای دخیل در ساخت فلز اطلاق میشود. برای شکلدهی فلز میبایست به آن تنش وارد کرد تا استحکام آن به چالش کشیدهشود. وقتی تنشی به فلز وارد شود، فلز به آرامی به آن پاسخ و تغییر شکل میدهد.
به طور کلی فلز میتواند تا حدی منقبض شود، کش بیآید و یا خم شود. میزان این تغییرات با میزان نیروی وارده متناسب خواهد بود. همچنین وقتی نیرو از بین برود فلز به حالت قبلی خود باز خواهد گشت. به این حالت تغییرشکل ارتجاعی یا کشسانی میگویند. و وقتی میزان نیروی وارده از حدی بیشتر شود، فلز به حالت قبلی خود باز نمیگردد که به این حالت تغییرشکل پلاستیکی یا مومسانی میگویند. در حالت تغییرپذیری دیگر تغییرات شکل فضایی با نیروی وارده متناسب نخواهد بود . همچنین این تغییرات بعد از آزاد شدن نیرو باقی میمانند و شکل فلز به حالت اولیه خود باز نمیگردد.
محدوده متناسب یا حد تناسب
نقطهای که تغییرشکل اکشسان به مومسان تبدیل میشود، محدوده متناسب نام دارد و اغلب تعیین آن مشکل است. برای مشخص کردن این نقطه معمولا در عمل از میزان جابجایی ۰٫۰۰۲ استفاده میکنند.
همان طور که درنمودار مشخص است وقتی تنش از میزان محدوده متناسب عبور کند، میزان بیشتری نیرو برای تغییرشکل نیاز است. در واقع هرچقدر فلز بیشتر تغییر کند، مستحکمتر میشود. به این حالت، کرنشسختی یا کارسختی میگویند که در فرایند شکلدهی فلز بسیار حائز اهمیت است. در بیشتر موارد کرنشسختی مانعی است که باید به آن غلبه کرد اما اگر به درستی از آن استفاده شود کاربردی حیاتی در فرایند ساخت خواهد داشت، مخصوصا در تولید قطعات مستحکم.
تنش سیلان
در طول فرایند تولید و شکلدهی فلز لازم است تا نیرو و انرژی به کار رفته را بشناسید. همانطور که گفتهشد پس از عبور از یک نقطه خاص نیروی بیشتری برای ایجاد تغییرات در فلز لازم است. تنش سیلان میزان نیرویی است که در هر لحظه از فرایند برای ادامه تغییر شکل فلز نیاز است. این میزان نتیجه عملکرد کشش است و میتوان برای بررسی لحظهای فرایند شکلدهی از میزان گردش تنش استفاده کرد. حداکثر میزان تنش لازم نقش مهمی در فرایند تولید دارد چرا که حداکثر نیروی لازم برای ایجاد تغییرات را مشخص میکند. برای مشخص کردن حداکثر تنش سیلان میبایست ابتدا حداکثر کشش را محاسبه کرد.
برای دیگر انواع تغییر شکل ممکن است بررسی تنش سیلان متفاوت باشد. در فرایندی مثل آهنگری میزان تنش سیلان بسیار مهم است. اما در فرایندی مثل فشارکاری یا اکستروژن که فلز دائما در حال تغییر شکل است و مراحل مختلف تغییرات همزمان با هم رخ میدهند، بررسی میانگین گردش تنش اهمیت دارد.
ممکن است علاقه مند باشید تا مطالعه کنید: فرایند فشارکاری (اکستروژن) آلومینیوم
نرخ کرنش
در فرایند ساخت و تغییر شکل هر فلزی، نرخ کرنش مستقیما مرتبط با سرعتی است که تغییر شکل در آن رخ میدهد. هرچه نرخ تغییر شکل قطعه فلزی بیشتر باشد، نرخ کرنش هم بیشتر است. نوع فرایند مورد استفاده و ویژگیهای فیزیکی قطعه مورد نظر، ارتباط زیادی با نرخ کرنش دارند. نرخ کرنش بر میزان گردش تنش اثر میگذارد و این تاثیر به نوع فلز و دمای فرایند وابسته است. در شکل زیر رابطه گردش تنش و نرخ کرنش یک فلز معمولی در دماهای مختلف نشان داده شده است.
اثر گرما در شکلپذیری فلز
ویژگیهای فلز بعد افزایش دما تغییر میکند. فلز در دماهای مختلف پاسخ متفاوتی به یک نوع فرایند مشخص میدهد و همچنین ممکن است که بخشهای مختلف هم ویژگیهای مختلفی از خود نشان دهند. به همین دلیل لازم است تا مواد مورد استفاده در روند ساخت از جمله رفتار آنها در دماهای مختلف را به خوبی بشناسیم. در فرایندهای صنعتی شکلدهی فلز سه محدوده دمایی وجود دارد که فلز در آنها تغییر شکل داده میشود. این محدودهها شامل سرد، گرم و داغ میشوند.
ممکن است علاقه مند باشید تا مطالعه کنید: عملیات حرارتی : انواع فرآیندهای عملیات حرارتی
کارسرد
کارسرد یا تغییرشکل سرد یک نوع فرایند شکلدهی فلز است که در دمای اتاق یا کمی بیشتر از آن انجام میشود. تغییرفرم الاستیک در این فرایند سبب ایجاد کرنشسختی میشود که قبلا به آن اشاره شدهبود. کارسرد در دماهایی پایینتر از محدوده تناسب انجام میشود. درنتیجه، در طیف دمایی کارسرد نسبت به کارگرم و کارداغ، نیروی بیشتری برای شکل دادن به یک قطعه نیاز است. همچنین، در کارسرد رسانایی و میزان شکل پذیری فلز محدودتر است.
آماده سازی سطح در کارسرد مهم است چرا که ترکخوردن ماده ممکن است میزان تغییرشکل را محدود کند. در واقع بعضی مواد در کارسرد ترک میخورند و میبایست کارگرم شوند. این فرایند به جز مشکلاتی مثل کاهش رسانایی دارای مزایای زیادی است. به علت کرنشسختی، قطعه سختتر و محکمتر خواهد بود. کارسرد میتواند رگههایی در جهتهای مختلف ایجاد کند که میتوان با کنترل کردن آنها به استحکام فلز افزود.
اگر با فرایند سردکاری، فلزی را پرداخت کنید، محصولی با اشکال هندسی دقیقتر و ظرافتهای سطحی بهتر تولید خواهید کرد. از آنجاییکه این فرایند نیازی به گرمادهی ندارند میتوان زمان و انرژی زیادی را ذخیره کند. با این که به فشار زیادی نیاز است اما در مجموع انرژی لازم برای سردکاری کمتر از گرمکاری است.
کارگرم
کارگرم یا شکلدهی گرم در دمایی بالاتر از دمای سردکاری و پایینتر از دمای تبلور مجدد فلز انجام میگیرد. این فرایند ممکن است به دلیل نیاز به نیروی کمتری نسبت به سردکاری، ترجیح داده شود. همچنین میزان بازپخت لازم برای گرمکاری کمتر از سردکاری است.
کار داغ
داغکاری یا شکلدهی داغ در دمایی بالاتر از دمای تبلور مجدد فلز صورت میگیرد. به دلیل بالاتر بودن دما از نقطه تبلور رفتار فلز بسیار متفاوت خواهد بود. یکی از جنبههای این فرایند به کارگیری ویژگیهای مختلف فلز در این دما است. دمای منفذ و دستگاه مورد استفاده در بیشتر فرایندها خنک یا مقداری گرم است. در کارگرم نیز دمای این بخش باید به نسبت بیشتر از دمای فلز باشد.
در طراحی فرایندهای شکلدهی، کنترل مسیر حرکت فلز بسیار اهمیت دارد. تفاوت دمای میان دستگاه و فلز در حرکت فلز نقش خواهد داشت. در واقع بخشهایی از فلز که به دستگاه نزدیکتر هستند، سختتر حرکت میکنند و هرچه میزان این تفاوت بیشتر باشد، کار سختتر خواهد شد. حفظ دماهای بالاتر در طول فرایند شکلدهی سختتر است. خنکسازیها هم ممکن است سبب تفاوتهای دمایی بیشتر شوند.
یکی دیگر از نگرانیها این است که هر چه قدر دما بیشتر باشد فلز واکشپذیرتر شود. اگر در بعضی قسمتها گرما بیش از حد زیاد شود، اصطحکاک افزایش مییابد و ممکن است که آن قسمت ذوب شود. در فرایند شکلدهی داغکاری حداکثر دما میبایست بر اساس نوع فلز و فرایند مورد استفاده تعیین شود.
مزایا و معایب کار داغ
در دمای بالاتر از دمای تبلورمجدد،استحکام فلز کم میشود و کرنشسختی هم رخ نمیدهد؛ چرا که فلز تغییرحالت برگشتپذیر کردهاست. شکلدهی فلز در داغکاری نیاز به انرژی و نیروی کمتری نسبت به سردکاری دارد. در دمای بالا رسانایی هم بیشتر میشود که امکان تغییر شکلهای بیشتری را که در سرکای ممکن نبوده است فراهم میکند.
بعد از اتمام فرایند و سرد شدن، فلز دوباره تبلور مییابد. به طور کلی داغکاری جاهای خالی و منافذ را میبندد، فولاد را با پخشکردن یکدست میکند و رگههای قدیمیتر را از بین میبرد. این فرایندها، افزایش دما سبب کرنشسختی نشده و رسانایی شکلگرفته در ماده را کاهش نمیدهند. کرنشسختی یک بخش ممکن است مطلوب و یا نامطلوب باشد که به کاربرد فلز وابستهاست. ویژگیهای فرایندهای شکلدهی گرم که به عنوان نقاط ضعف شمرده میشوند شامل کیفیت کم سطح فلز، وسعت زیاد و اکسایش، کربنزدایی، کمتر بودن دقت هندسی و نیاز به گرم کردن قطعات است. گرم کردن قطعات طول عمر آنها و بازدهی را کمتر و نیاز به انرژی را بیشتر میکند.
انتخاب بازه دمایی برای عملیاتهای شکلدهی فلز
ساخت فلز در هر بازه دمایی مزایا و معایب خود را دارد. بعضی وقتها ویژگیهایی که برای یک فرایند نامطلوب هستند، برای دیگر فرایندها مطلوب هستند. گاهی بخشهای مختلف یک محصول نیازهای مختلفی دارند. هدف این است که فرایند ساخت یک بخش از محصول را به گونهای موثر طراحی کنیم.
برای ساخت قطعات مستحکم با ظاهر سطحی خوب، سردکاری انتخاب خوبی است. اما برای ساخت یک قطعه با رسانایی بالا باید به سراغ داغکاری رفت. گاهی در هنگام ساخت یک قطعه، از یک سری فرایندهای گرم و سر استفاده میکنند. برای مثال ممکن است داغکاری ابتدا روی یک قطعه اجرا شود تا به میزانی از تغییر شکل برسیم که به علت کرنشسختی و رسانایی محدود سردکاری ممکن نبوده است. در ادامه میتوان سردکاری را در پیش گرفت که نیازی به تغییرات زیادی ندارد و تغییرات را پایان میدهد، قطعه را محکم میکند و ظاهر خوبی ایجاد میکند.
اصطکاک و گریسزنی در شکلدهی فلز
شکل فلز نقش مهمی در تعامل بین دو صفحه در فشار بالا دارد. در عملیاتهای شکلدهی داغ، فشار زیاد از طریق دماهای فوقالعاده بالا ایجاد میشود. اصطکاک بین فلز و دستگاه اهمیت زیادی دارد. مقداری اصطکاک در ساخت فلز لازم است اما مقدار بیش از حد آن همیشه نامطلوب است. اصطکاک نیروی لازم را افزایش میدهد، سبب فرسوده شدن وسایل میشود، حرکت فلز را مشکل میکند و روند کار را معیوب میکند.
وقتی اصطکاک وجود داشته باشد، گریسزنی کمککننده است. گریسزنی برای بعضی قطعات به کار نمیرود ولی برای کاهش اصطکاک بین بسیاری از صفحات به کار میرود. نوع گریس، روانکننده و یا روغنی که در صنعت به کار میرود، به نوع فلز، دمای فرایند و نوع ماده تشکیلشده بستگیدارد. انواع روانکنندهها شامل روغنهای گیاهی و معدنی، صابون، گرافیت پخششده در گریس، محلولهای آبی، پلیمرهای جامد، واکس و شیشه ذوب شده است.
انواع مختلف فرایندهای شکلدهی فلز
این فرایندها را میتوان به دو گروه فرایندهای اصلی تغییرشکل تودهای و ورقکاری فلزی تقسیمکرد. در تغییرفرم تودهای بر خلاف ورقکاری نسبت سطح به حجم کم است.
تغییر شکل یا تغییرحالت تودهای
نورد: نورد یک فرایند تغییر شکل فلزات است که با استفاده از غلتکها انجام میشود. فرایندهای نورد شامل مواردی همچون نورد دو غلتکه، سه غلتکه، چهار غلتکه و نورد پنج غلتکه میشوند.
آهنگری: در این روش از یک سری منافذ برای فشردن و شکلدهی به قطعه فلز استفاده میشود. این منافذ ممکن است صاف یا دارای شکل خاصی باشند.
اکستروژن یا فشارکاری: شامل وارد کردن فلز به درون ورودی یک منفذ میشود و نتیجه آن تولید قطعات با طول متفاوت و سطح مقطع یکسان است.
بیرونکشیدن: این روش مشابه بیرونانداختن است و در آن قطعه با طول مشخص وارد یک منفذ میشود و سطح مقطع مورد نظر آن شکلدادهمیشود. در این روش کاربرد نیرو با بیرونانداختن متفاوت است. در بیرون انداختن قطعه با فشار وارد منفذ میشود ولی در بیرونکشیدن قطعه از درون منفذ بیرون کشیدهمیشود.
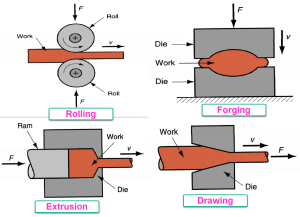
ورقکاری فلزی
شکافتن یا برش: این روش شامل بریدن و سوراخ کردن قطعه فلز میشود. از نظر فنی شکافتن شامل تغییرحالت مومسان نمیشود اما در بین فرایندهای ورقکاری فلزی دارای اهمیت است و باید همراه آنها شناخته شود.
خمکردن: این روش یک نوع تغییرفرم از طریق خم کردن قطعه فلز در یک جهت خاص میشود.
بیرونکشیدن یا کشش عمیق: در این نوع فرایند شکلدهی یک قطعه صاف صفحه یا ورقه با فشار وارد یک حفره میشود تا شکل خاصی مثل یک فنجان را به خود بگیرد.
سخن پایانی
روشهای شکلدهی گفته شده و محصولات آنها دارای مزایای و ضعفهای مختلفی هستند. اما برای بیشتر مصرفکنندگان در دسترس بودن و آسان بودن تولید عامل تعیینکننده برای استفاده از هر یک از این روشها است.
برخی واژه های تخصصی
شکلدهی فلز: metal forming
تغییرشکل کشسان: elastic deformation
تغییرشکل مومسان: plastic deformation
کرنشسختی: strain hardening
حد تناسب: proportional limit
کارسختی: work hardening
تنش سیلان: flow stress
نرخ کرنش: strain rate
کارسرد: cold working
کارگرم: warm working
بازپخت: annealing
کارداغ: hot working
دمای تبلور مجدد: Recrystallization Temperature
تغییرشکل تودهای: bulk deformation
ورقکاری فلزی: sheet metal working
آهنگری: Forging
اکستروژن یا فشارکاری: Extrusion
بیرونکشیدن: Drawing
شکافتن یا بریدن: Shearing
خمکردن: Bending
بیرونکشیدن یا کشش عمیق: Deep Drawing
Comment (1)
مقاله کاملی بود ممنون از شما