آشنایی با مشخصات فلز روی ( Zinc ) و کاربرد آن در صنعت
مشخصات فلز روی
روی عنصر فلزی براق به رنگ سفید مایل به آبی است. در دمای معمولی به حالت شکننده و کریستالی است اما در دمای بین C°۱۵۰-۱۱۰ خاصیت چکش خواری و تورق دارد. از لحاظ فراوانی، روی بیست و سومین عنصر موجود در لایه پوسته زمین میباشد. روی فلزی است به رنگ سفید متمایل به آبی که بر اثر رطوبت هوا تیرهرنگشده و در حین احتراق، رنگ سبز براقی تولید میکند. روی بعد از آهن، آلومینیوم و مس چهارمین فلز پر استفاده در جهان میباشد.
منابع اصلی آن معدن سولفید، زینکبلند یا اسفالریت زینکیت ، کالامین ( سیلیکات روی ) و اسمیت سونیت ( کربنات روی ) می باشند. سنگ سولفیدی برای تبدیل شدن به اکسید برشته شده و با زغال تا دمای C°۱۲۰۰ حرارت داده می شود. سپس تبخیر و خارج از محفظه واکنش متراکم شده و در قالب هایی که اسپلتر نامیده می شود قالب گیری می شود.
روش استخراج روی ـ خاک روی از سوختن و اکسید شدن سنگ معدن روی و واکنش اکسید روی با زغال یا کربن توسط تقطیر فلز حاصل می شود. روی در طبیعت دارای ۵ ایزوتوپ پایدار است و ۱۶ عدد ایزوتوپ ناپایدار نیز برای روی شناخته شده است.
« با خواص و کاربردهای خاک روی بیشتر آشنا شویم »
این عنصر خاصیت نیمه رسانا دارد و در هوا با شعله قرمز خیلی داغ می سوزد و ابرهای سفید سمی از آن ساطع می شود. خاصیت قالب پذیری این عنصر بالا است. نه فلز روی نه زیرکونیم هیچ کدام خاصیت آهنربایی ندارند. اما این ترکیب ZrZn2 در دمای زیر ۳۵۰ درجه کلوین خاصیت آهنربایی دارد.
این فلز دارای آلیاژهای زیادی می باشد که شامل برنج ( مشخصات فلز برنج )، نقره نیکلی ، برنز تجارتی ، لحیم قلع ، آلومینیوم لحیم شده است. روی با کیفیت بالا برای تولید قالب استفاده می شود که از این قالب گیری برای کاربردهای اتومبیل سازی و صنایع الکتریکی و سخت افزارها استفاده مي شود.
یک آلیاژ روی که به نام پرزتال (آشنایی با مشخصات آلیاژ زاماک ( Zamak ) و کاربرد آن در صنعت ) نامیده می شود شامل ۷۸ درصد روی و ۲۲ درصد آلومینیوم است که بیشتر در صنایع فولاد و پلاستیک های قالب گیری كاربرد دارد. از این آلیاژ همچنین برای قالب گیری سرامیک و سیمان نيز استفاده می شود. خواص آلومینیوم در ترکیب با روی باعث می شود که این آلیاژ از آلیاژهای پرکاربرد آلومینیوم شده و کاربردهای زیادی داشته باشد.
روی همچنین جهت جلوگيری از خوردگی برای آبکاری دادن فلزاتی مثل آهن نيز استفاده می شود. اکسید روی در دنیای مدرن فلز مفيدی محسوب می شود. از جمله کاربردهای اکسید روی در صنایع و ساخت رنگ ها، تولیدات لاستیک، وسایل آرایشی و صنایع داروسازی، پوشش کف، پلاستیک، چاپ پارچه، صابون سازی، ذخیره باتری ها، منسوجات، تجهیزات الکتریکی و دیگر تولیدات می باشد.
لیتوفون ترکیبی از سولفید روی و سولفات باریم است که برای تولید مواد و رنگدانه ها مورد استفاده قرار می گیرد. سولفید روی در ساختن صفحات روشن و تابناک، صفحات اشعه ایکس و تلویزیون و نورهای فلورسانس مورد استفاده قرار می گیرد. از ترکیبات کلر و کرومات روی برای ترکیبات مهم استفاده می شود. روی عنصر حیاتی برای رشد و نمو جانوران و گیاهان است.
روی به تنهایی و به خودی خود سمی نیست اما وقتی که با اکسیژن هوا ترکیب می شود به ماده سمی تبدیل می شود که تنفس را دچار مشکل می کند که در موقع استفاده از آن باید دقت لازم را به عمل آرود. غلظت اکسید روی در موقع کار در آزمایشگاه، اگر تهویه لازم نداشته باشد، نبايد از ۵ mg/m3 تجاوز کند.
مشخصات روی |
|||
اولین انرژی : ۲ | دومین انرژی : ۸ | سومین انرژی : ۱۸ | چهارمین انرژی : ۲ |
عدد اتمی : ۳۰ | رنگ : سفید مایل به آبی | حالت اکسیداسیون : ۲ |
اشکال دیگر :
|
جرم اتمی : ۶۵٫۴۰۹ | حالت استاندارد : جامد | گرمای تبخیر : Kj/mol 115.3 | |
نقطه ذوب : C °۴۱۹٫۷۳ | نام گروه : ۱۲ | شماره سطح انرژی : ۴ | |
نقطه جوش : C °۹۰۷ | شعاع یونی : A °۰٫۷۴ | گرمای فروپاشی : Kj/mol 7.322 | |
شعاع اتمی : A °۱٫۵۳ | ظرفیت : ۲ | انرژی یونیزاسیون : Kj/mol 9.394 | |
دوره تناوبی : ۴ | دانسیته : ۷٫۱۳ | الکترونگاتیوی : ۱٫۶۵ |
سابقه تاريخی فلز روی در جهان
قديمی ترين قطعه ساخته شده از روی بتی است كه در كاوش های باستان شناسی در” دردوش “( Dordosh ) در منطقه ترانسيلونيا به دست آمده و در تركيب آن ۵۲/۸۷ در صد روی ، ۴۱/۱۱ درصد سرب و ۰۷/۱ درصد آهن وجود داشته است. در خرابه های كامرس ( Cameros ) كه ۵۰۰ سال قبل از ميلاد ويران شده است دستبندی به دست آمده است كه از روی پر شده بود.
۲۰۰ سال بعد از ميلاد، رومی ها با برنج آشنا شدند و آن را به روش ذوب و احياء در كوره و به همراه مس (مشخصات فلز مس) شكل می داده اند. در طول اين فرآيند نخست اكسيد روی احياء می گرديد. سپس بخارات روی در مس نفوذ می كرد و با افزايش دما، محصول ذوب شده و برنج با تركيب يكنواخت حاصل میشد.
روی به صورت فلز و به صورت اكسيد روی از قرن ۱۲ ميلادی در هندوستان توليد شد و بعدها در قرن هفدهم در كشور چين توليد و مورد استفاده قرار گرفته است. در حدود سال ۱۷۳۰ دانش ذوب روی از چين به انگلستان رسيد و در سال ۱۷۳۹ امتيازنامه برای فرآيند تقطير به ثبت رسيد و در طول سال های ۱۷۴۳ – ۱۷۴۰ يک كارخانه ذوب روی با توليد ۲۰ تن در سال در بريستول احداث و راه اندازی گرديد. اين فرآيند شامل مخلوط كربن و سنگ معدن اكسيد روی بوده که در يک كوره كه ته آن لولهای تعبيه شدهبود، مورد استفاده قرار میگرفت و روی تبخير شده در لوله مايع میشد و در خارج كوره جمع آوری میگرديد.
در ايالات متحده امريكا روی برای نخستين بار در سال ۱۸۳۵ در واشنگتن توليد شد. در سال ۱۸۸۰ هيدرومتالورژی روی برای توليد سولفات روی ( ترکیبات سولفات روی ) و استفاده از آن برای توليد رنگدانه Lithapone معمول بوده است. تا حدود سال های ۱۸۸۰ به كانه های سولفوره روی چندان توجهی نمی شد و در اروپا اغلب كالامين برای توليد روی مورد استفاده قرار می گرفت. لكن در طول سال های ۱۸۸۱ فرآيند تصفيه اصلاح گرديد و گاز So2 با درصد بالا حاصل شد و بدين ترتيب سنگ های سولفوره در مدار توليد روی قرار گرفت.
سابقه تاریخی فلز روی در ایران
قديمی ترين گزارش های مدون معدنی در ايران مربوط به معدن فيروزه نيشابور و مس قلعه زری است كه قدمت آن به ۴ تا ۵ هزار سال قبل از ميلاد مسيح می رسد. كليه فعاليت های معادن سرب و روی تا قبل از جنگ جهانی دوم تقريبا به شكل باستانی انجام می شده است. در دهه ۱۹۳۰ كارشناسان آلمانی شيوه معدنكاری جديد را به خصوص در زمينه معادن فلزی به ايران آوردند.
در اين زمان معادن سرب و روی نخلک ، سياه كوه انارک ، سرب بی بی شهربانو و چند معدن ديگر فعال بودند. معادن سرب و روی در سال های ۱۳۴۶ الی ۱۳۵۶ از رونق خوبی برخوردار بودند. اولين كارخانه تغليظ سرب و روی به روش مدرن در سال ۱۳۴۰ با كمک يک شركت فرانسوی در لكان استان مركزی مورد بهره برداری قرار گرفت. از سال ۱۳۴۲ تا ۱۳۷۲ محصول معادن روی ايران بعد از فرآوری به صورت كنسانتره به خارج از كشور صادر می شده است. در کشور ایران معادن سرب و روی دارای اهمیت زیادی هستند که شما می توانید در بخش لیست معادن سرب ایران و لیست معادن روی ایران به بررسی هر یک بپردازید.
بعد از جنگ تحميلی، با توجه به وجود معدن انگوران ديدگان متخصصان داخلی به كسب تكنولوژی فلز روی معطوف گرديد و در اين رابطه تحقيقات گسترده ای در سطح ملی برای كسب تكنولوژی توليد شمش روی از كنسانتره و سنگ معدن انگوران انجام و منجر به توليد اولين شمش روی در مقياس پايلوت در سال ۱۳۷۱ گرديد.
از سال ۱۳۷۲ نيز توليد شمش روی در شركت فرآوری مواد معدنی ايران ( واحد ذوب زنجان ) شروع و از آن تاريخ به بعد با احداث و راه اندازی واحدهای جديد، توليد شمش روی در كشور سير صعودی را طی نمود. اين واحد عمدتا با استفاده از تكنولوژی اكتسابی داخلی به توليد شمش روی مشغول می باشند.
روی ، رخدادی طبیعی
در طبيعت دو عنصر سرب و روی ، اغلب با هم همراهند و اگر با مشخصات فلز سرب و همینطور مشخصات فلز روی آشنایی داشته باشید، می دانید که سنگ های درونگير مشتركی دارند. نزديک به ۷۰ درصد سرب معدنی از كانه های مخلوط سرب و روی كه به طور معمول مقادير روی در آنها بيشتر از سرب است، توليد می شود. نزديک به ۲۰ درصد از توليد سرب مربوط به كانه های مخلوطی است كه مقدار سرب در آن ها از روی بيشتر است و ۱۰ درصد بقيه توليد سرب در رابطه با كانی های مس دار است.
كانی های سرب و روی غالباً به صورت مخلوط و كانسارها ديده می شوند. كانسارهای اصلی اين دو فلز از نوع گرمابی به صورت اپی ترمال، مزوترمال و تله ترمال هستند. در كانسارهای مزوترمال معمولاً مقدار روی بيشتر است. كانسارهایی كه به صورت گرمابی تشكيل شدهاند بسته به نوع جا گذاشتن سرب در شكاف ها و درزه ها به گروه های انباشتی كه در آن سرب موجود در محلول گرمابی به علت فعل و انفعالات شيميايی به املاح نامحلول تبديل و درزه ها و شكاف ها را انباشته می كند و جانشينی كه در آن يون سرب موجود در محلول گرمابی با يون فلزات موجود در سنگ های اطراف جانشين شده و مثلاً كربنات كلسيم يا آهک را به كربنات سرب تبديل می كند، تقسيم می شوند.
كانی های سولفوره سرب و روی در قسمت بالای كانسارها تحت تأثير آب و هوا قرار گرفته، دگرسان شده و به كانی های اكسيده اين فلز تبديل می شوند. لازم به ذكر است كه اسفالريت زودتر از گالن دگرسان می شود. توده های تله ترمال معمولاً در طبقات آهكی در قسمت هايی كه رگه ها گرمابی نمی شوند وجود دارند.
در محل اين توده ها تبلور مجدد كلسيت و دولوميت مشاهده شده و گاهی كمی گچ و باريتين همراه كانه می شود، در اين كانسارها گاهی آهک هم كمی سيليسی می شود. كانسارهای تله ترمال معمولاً از نوع جانشينی اند.
روی عموماً به صورت سولفيد و در بيشتر مواقع از منشأ سيالات گرمابی و ماگماهای سياليک و سيميک رخ می دهد. كانسارهای رسوبی اهميت كمتری دارند. تعدادی از كانسارهايی كه در كربنات ها تشكيل می شوند، خواص كانسارهای رسوبی دريايی را دارا هستند. اگر چه در اين كانسارها می توان چنين فرض كرد كه فلز از اين طريق انتقال گرمابی از ماگماهای بازی تأمين شده است.
انباشته های قابل بهره برداری روی در محيط های زمين شناختی گوناگون يافت می شوند. اين انباشته ها بر حسب شرايط پيدايش از نظر زمين شناختی به بخش های ذيل تقسيم می شوند :
- سولفورهای توده ای ناشی از فوران های زير دريايی موجود در سنگ های رسوب
- انباشته های چينه كرانی در سنگ های كربناتی
- انباشته های چينه كران در ماسه سنگ ها
- رگه ای
- انباشته های دگرگونی
ترکیبات روی
ترکیبات روی بخش مهمی از تولیدات صنایع روی را تشکیل میدهند. مواد شيميايی با بنيان روی شامل غبار روی ۱۲ تا ۱۵ درصد مصرف روی جهان را در اختيار دارد. اكسيد روی به طور كمی مهمترين محصول شيميايی با بنيان روی می باشد. غبار روی سولفات روی و كلريد روی، از نظر اهميت و كميت در رده های بعدی قرار دارند.
ساير تركيبات روی دارای اهميت فرعی می باشند. سال هاست كه مصرف جهانی اكسيد و غبار روی ثابت مانده است، اگر چه تقاضا جهت سولفات روی و كلريد روی در حال افزايش است. سرعت رشد مصرف تيوكربنات روی و استيرات روی بر توليد سايندهها ( بزرگترين مصرف اين تركيبات ) منطبق است. اكسيد روی كه دارای بيشترين تقاضاست را می توان با فرايندهای متنوعی توليد نمود.
خلوص و كيفيت اكسيد روی به روش توليد آن بستگی دارد. اكسيد روی با خلوص بالا به صورت پودر در اتاق های رسوب، در جايی كه ذرات با اندازه های مختلف از هم جدا می گردند، جمع می شود. اين ماده عموماً به عنوان روی سفيد شناخته می شود. در فرايند مستقيم ( يا فرايند آمريكايی ) ماده خام استفادهشده، كانه روی يا محصولات جانبی روی بوده كه همواره حاوی سرب می باشد. يک ماده كربن دار را با ماده خام حرارت می دهند كه در نتيجه احياء، روی به صورت بخار احيا می شود. اين ماده در هوا اكسيد شده و به ذرات با اندازه مختلف تقسيم می شود.
اصلیترین ترکیبات روی عبارتند از :
- هیدریدروی (ZnH۲)
- اکسیدروی (ZnO)
- کلریدروی (ZnCl۲)
همچنین، این فلز دارای آلیاژهای زیادی میباشد که شامل برنج، نقره نیکلی، برنز تجارتی، لحیم قلع، آلومینیوم لحیمشده است. روی با کیفیت بالا برای تولید قالب استفاده می شود که از این قالب گیری برای کاربردهای اتومبیل سازی و صنایع الکتریکی و سخت افزاها استفاده می شود. یک آلیاژ روی که به نام پرزتال ( آشنایی با مشخصات آلیاژ زاماک ( Zamak ) و کاربرد آن در صنعت) نامیده میشود شامل ۷۸ درصد روی و ۲۲ درصد آلومینیوم است که بیشتر در صنایع فولاد و پلاستیک های قالبگیری كاربرد دارد. از این آلیاژ همچنین برای قالبگیری سرامیک و سیمان نيز استفاده می شود.
روی همچنین جهت جلوگيری از خوردگی برای آبکاری دادن فلزاتی مثل آهن نيز استفاده میشود. اکسید روی در دنیای مدرن فلز مفيدی محسوب می شود که به طور گستردهای برای صنایع و ساخت رنگها، تولیدات لاستیک، وسایل آرایشی و صنایع داروسازی، پوشش کف، پلاستیک ، چاپ پارچه، صابونسازی، ذخیره باتریها، منسوجات، تجهیزات الکتریکی و دیگر تولیدات کاربرد دارد. لیتوفون ترکیبی از سولفید روی و سولفات باریم است که برای تولید مواد و رنگدانه ها مورد استفاده قرار میگیرد.
سولفید روی در ساختن صفحات روشن و تابناک، صفحات اشعه ایکس و تلویزیون و نورهای فلورسانس مورد استفاده قرار میگیرد. از ترکیبات کلر و کرومات روی برای ترکیبات مهم استفاده میشود. روی عنصر حیاتی برای رشد و نمو جانوران و گیاهان است.
ماده اوليه جهت فرايندهای شيميايی مرطوب محلول های خلوص يافته روی است. كربنات يا هيدروكسيد روی، ته نشين شده و سپس فيلتر شده شسته، خشک و در دمای ۸۰۰ درجه سانتی گراد به صورت پودر در می آيد.
انواع متنوع اكسيد روی به عنوان محصول واسطه در توليد ساير مواد شيميايی استفاده می شود. اكسيد روی ته نشين شده كه دارای خواص رنگريزه ای نمی باشد و درجه های ويژه مانند اكسيدهای روی ظريف كه در كاغذهای فتوكپی كاربرد دارد. مهمترين كاربرد اكسيد روی در صنعت ساينده هاست، كه در اين صنعت به عنوان فعال ساز سخت كننده و برخی اوقات به عنوان فيلتر استفاده می شود.
اكسيد روی به عنوان رنگريزه در رنگ های لاتكس محلول كاربرد فراوانی دارد. كاربرد اين ماده در كشاورزی به عنوان افزاينده بارور كننده جهت جبران كمبود روی خاک از اهميت كمتری برخوردار است. اكسيد روی جزئی از فرمولاسيون در صنعت شيشه، لعاب كاری و سراميک می باشد. اين ماده بر روی نقطه ذوب، خواص نوری و الاستيک و همچنين رنگ و جلای شيشه ها تاثير می گذارد. اكسيد روی يكی از تشكيل دهنده های پودر صورت، رژ لب و كرم های است كه در صنعت لوازم آرايشی كاربرد دارد می باشد. اين ماده همچنين به عنوان افزاينده به روغن، چسب، عامل های خشک كننده، عامل های غير شفاف ساز و به عنوان كاتاليزور در سنتز متانول كاربرد دارد.
کشورهای تولیدکننده روی در جهان
استرالیا ، چین ، پرو ، مکزیک و آمریکا بزرگترین ذخایر روی جهان را در اختیار دارند که جمعا حدود ۱۵۲ میلیون تن ( معادل ۷۴ درصد ذخایر جهان ) را شامل می شود. البته کانه روی در بیش از ۵۰ کشور یافت شده است. چین با تفاوت فاحشی نسبت به استرالیا و پرو بزرگترین عرضه کننده روی می باشد و علاوه بر آن مصرف کننده عمده برای این فلز است.
فرآوری و استخراج روی
روشهای تولید روی به طور کلی به دو دسته پیرومتالورژیکی و هیدرومتالورژیکی تقسیم میشوند. حدود ۸۵-۹۰ درصد روی تولیدی در جهان به روش هیدرومتالورژی است.
۸۰ درصد معادن روی در زیر زمین، ۸ درصد به صورت روباز و مابقی به صورت ترکیبی از دو حالت روباز و زیرزمینی هستند. از لحاظ حجم تولید فلز روی ، ۶۴ درصد از معادن زیرزمینی ( پوشیده )، ۱۲ درصد معادن روباز و ۱۵ درصد از معادن ترکیبی به دست میآید.
در مورد سایر فلزات به ندرت تولید فلز از خاک به طور مستقیم انجام میشود. برای انجام فرآیند تغلیظ، خاک معدنی خردایش شده و سپس جداسازی سایر فلزات انجام می شود. به صورت معمول کنسانتره روی با غلظت % ۵۵، از کمی سرب ، مس و آهن تشکیل میشود. فـرآیند تغلیظ اغلـب در محـل معدن انجام میشود تا هزینههای حمل و نقل به حداقل برسد.
تشویه و زینترینگ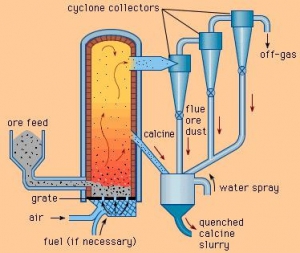
بیش از ۹۵ % از روی تولیدشده جهان از سولفید روی تولید میشود، کنسانتره روی معمولاً از %۳۰-۲۵ گوگرد و مقــادیر مختلـفی از سایر فلزات مانند آهـن، سـرب و نقره است که قـبل از آنکه فلز روی به وسیله تکنیک های هیدرومتالوژی و پیرومتالوژی استحصال شود، گوگرد موجود در آن باید جداسازی شود. این کار از طریق تشویه و یا از طریق زینترینگ انجام می شود.
در این کار کنسانتره روی تا دمای بالا حرارت داده می شود و سولفور روی به اکسید روی اکتیو تبدیل میشود و بلافاصله بعد از آن میتوان اسید سولفوریک تولید کرد که یک محصول اقتصادی است.
به منظور استفاده از سولفید روی نیاز به سیستم تشویه بوده و هزینه مستقیم تشویه تقریباً برابر با هزینههای کل قسمتهای کارخانه روی میباشد.
روش پیرومتالوژی
در روشهای پیرومتالورژی ماده معدنی فلز مورد نظر در دمای بالا و توسط تودههای مخصوص احیاء شده و استحصال میگردد. مکانیزم عمل فرایندهای پیرومتالورژیکی ایجاد حرارت زیاد و محیط مناسب برای انجام واکنش احیاء است.
در روشهای پیرومتالورژیکی تولید روی، اساس فرایند بر اساس واکنشهای زیر میباشد :
عامل احیاءکننده در این فرایند کک متالورژی بوده و از آهک برای کنترل بازیسیته استفاده میشود. دانهبندی مواد اولیه در این فرآیند بسیار مهم میباشد. در صورت استفاده از کنسانتره روی باید آن را به صورت گندله درآورد و در صورت استفاده از ماده معدنی اکسید روی، ابتدا باید آنرا به دانهبندی ۵-۱۰ میلیمتر رسانده و پس از انجام کلسیناسیون مورد مصرف قرار داد. عملیات کلسیناسیون طبق واکنش مقابل انجام میشود.
این عملیات بیشتر در کورههای دور (Rotary Kiln ) یا کورههای واگنی انجام میرسد. مرحله نهایی ذوب بر پایه کاهش روی و سرب با استفاده از کربن در کورههای خاصی که به همین منظور طراحی شده اند انجام می شود. این مرحله با توجه به مقدار بالای انرژی مصرفی بسیار هزینه زاست، امروزه این روش فقط در کشورهای چین ، هند ، ژاپن و لهستان مورد استفاده است.
روش هیدرومتالورژی
در روشهای هیدرومتالورژی ماده معدنی حاوی فلز مورد نظر در یک حلال مناسب حل شده و پس از جداسازی ناخالصیها، توسط جریان برق مستقیم و از طریق فرایند الکترولیز ( Electrowinning ) استحصال میگردد. در روشهای هیدرومتالورژیکی به دمای بالا نیاز نیست و استحصال فلز توسط واکنشهای الکتروشیمیایی انجام میشود.
فرایندهای هیدرومتالورژی عمدتا در دو روش خلاصه میشوند :
- روش مرسوم ( Conventional )
- روش استخراج انحلالی ( Solvent Extraction )
به دلیل ظرفیت محدود کورههای روش پیرومتالورژیکی، افزایش تعداد آنها جهت بالابردن ظرفیت مقرون به صرفه نمیباشد. لذا میزان تولید روی در دنیا با این روش محدود است و در صورتیکه فرآیندهای هیدرومتالورژیکی به دلیل امکان تولید اقتصادی و با ظرفیت بالا و همچنین به خاطر امکان استفاده از مواد اولیه با عیار پایین و ناخالصی زیاد، استفاده وسیعی در سطح جهان دارند.
در روش استخراج انحلالی ( Solvent Extraction ) که در این روش پس از انحلال ماده معدنی روی در اسیدسولفوریک، به کمک ماده آلی D2EHPA ، سولفات روی با خلوص قابل قبول و سطح ناخالصیهای مجاز به صورت انتخابی از محلول جدا شده و با تهیه محلول مناسب حاوی روی و با استفاده از جریان برق مستقیم در سلولهای الکترولیز ( Electrowinning ) فلز روی SHG ( Special High Grade ) با عیار بیش از ۹۹% روی استحصال میشود.
بررسی فرایند هیدرومتالورژی – روش مرسوم ( Conventional )
کنسانتره سنگمعدن، به واحد لیچ یا انحلال ( Leach ) منتقل میشود. در بخش انحلال مواد اولیه حاوی روی، با محلول برگشتی از واحد الکترووینینگ ( Spent ) در مخزنهای مخصوص به صورت پالپ ( Pulp ) در میآید. از محلول اسید سولفوریک تازه جهت تعادل سولفات ( مورد نیاز ) استفاده میشود. پس از لیچ اسیدی که با هدف انحلال حداکثر روی موجود در ماده معدنی انجام میشود، دوغاب حاصل به مخزن های لیچ خنثی پمپ میشود.
در این مخزنها با افزودن آب آهک، PH دوغاب جهت ایجاد شرایط مناسب برای ترسیب برخی از ناخالصیها مانند Si ، Fe ، Al ، Ge ،As و Sb و… افزایش مییابد. ناخالصیهای یاد شده به صورت جامد از محلول جدا شده و محلول جهت جداسازی سایر ناخالصیها به واحد تصفیه منتقل میشود. تصفیه محلول حاصل از لیچ طی سه مرحله انجام میشود.
در مرحله اول، غلظت یون کلر در محلول توسط کات کبود ( Cu SO4 ) تا حد مجاز کاهش مییابد. مرحله دوم شامل افزایش دمای محلول به ۷۰-۸۰ درجه سانتیگراد و افزودن پودر روی و تری اکسید آرسنیک، ناخالصیهای Cu ، Co و Ni به صورت کیک از محلول جداشده میباشد و محلول به مرحله بعد منتقل میشود. در مرحله نهایی با کاهش دما تا ۵۰ درجه سانتیگراد و افزودن پودر روی، کادمیوم به صورت اسفنجی از محلول جدا شده و محلول به برجهای خنککننده منتقل میشود.
در برجهای خنککن با کاهش دما حلالیت Ca ، Mg در محلول کاهش یافته و در نتیجه کریستالهای CaSO4 و MgSO4 شکل میگیرند و بر روی کف و دیواره برج خنککن و بخش داخلی مخزن ذخیره محلول، رسوب میکنند. محلول عاری از Ca و Mg به بخش الکترووینینگ هدایت میشود. در واحد الکترووینینگ، الکترولیت از سلولها عبور نموده و یون Zn2+ بر روی کاتد احیاء و نشسته میشود و پس از گذشت زمان مشخصی به صورت ورقه روی SHG استحصال میگردد.
ورقه روی حاصل، پس از کنده شدن از کاتد در واحد ورقهکنی، شسته شده و به واحد ذوب و ریختهگری منتقل میگردد. در واحد ذوب و ریختهگری، ورقها پس از خشکشدن به کوره القایی شارژ میشوند. سربارهگیری توسط کلرید آلومینیوم انجام میشود و مذاب روی به صورت شمش روی SHG ریختهگری میگردد. دقت در بهرهبرداری و تعدیل نمودن نوسانات کاری به خصوص در ظرفیتهای تولید بالا و بازیابی حداکثر میزان روی از جمله پارامترهای بسیار مهم در اقتصادی بودن فرآیند تولید روی بهشمار میآید.
چگونگی انحلال و خنثیسازی، مهمترین عامل در بازیابی روی میباشد. سیستم انحلال در نظرگرفتهشده جهت این طرح در برآورد نمودن دو هدف اصلی یعنی محلول خام مناسب جهت تصفیه و همچنین بازیابی بالای روی از ماده معدنی، میتواند بسیار موثر واقع گردد. به دلیل عدم آمادهسازی مواد، به خصوص عملیات فلوتاسیون سرب در ابتدای مدار و خارج نشدن برخی از کانیها از خوراک ورودی به فرآیند تولید روی، در اثر انحلال کانیهایی چون “میمیت” در اسید، میزان کلر در محلول افزایش مییابد.
بنابراین، به غیر از مرحله منیزیم زدایی که باعث کاهش غلظت منیزیم، کلر و فلوئور در مدار می گردد، یک مرحله کلرزدایی نیز در نظر گرفته میشود. به طور معمول با قرار دادن مراحل رسوبگذاری سولفات روی قلیایی (BZS ) (منیزیم زدایی) و مرحله حذف کلر سعی بر این است که غلظت کلر، فلوئور و منیزیم در غلظتی پایینتر از سطح مجاز نگه داشته شود.
لیچینگ ( انحلال )
-
لیچ اسیدی
پالپ با شدت جریان حجم معینی به مرحله لیچ اسیدی ارسال میگردد. قسمت اعظم پالپ ایجاد شده به همراه الکترولیت برگشتی، به مخازن مرحله لیچ اسیدی منتقل میشود. اسید سولفوریک تازه جهت تعادل سولفات مورد نیاز به این مرحله افزوده میشود. غلظت اسید در این مخزنها توسط کانه روی تنظیم میگردد. پارامترهای موثر در این مرحله از جمله درجه حرارت، زمان ماند و غلظت اسید سولفوریک به نحوی تنظیم میگردد که استحصال حداکثر فلز روی که مد نظر است امکانپذیر شود.
در این مرحله علاوه بر فلز روی سایر عناصر از جمله : کادمیوم، کبالت، نیکل، ژرمانیوم، فلوئور، کلر و غیره نیز در اثر انحلال وارد محلول لیچ میگردند. آهنی که از ته ریز تینکر مرحله اول خنثی سازی وارد این مرحله میشود توسط سولفات سدیم به صورت جاروزایت سدیم رسوب کرده و آرسنیک نیز به صورت اسکورودیت (FeAsO4 ) رسوب مینماید. دوغاب حاصل از لیچ اسیدی در تیکنر ته نشین شده و ته ریز تیکنر، پس از فیلتر شستشو شده و به مرحله عملیات پسماند ارسال میشود.
-
خنثی سازی
این عملیات در دو مرحله صورت میپذیرد. در مرحله اول سرریزتیکنر مرحله لیچ اسیدی توسط مقادیر مشخصی از خوراک پالپشده در مخازن این مرحله تحت شرایط معینی خنثیمیگردد. بعد از تهنشینی دوغاب این مرحله در تیکنر، سرریز تیکنر به برجهای خنککننده محلول و تهریز آن به مرحله لیچ اسیدی برگردانده میشود. در مرحله دوم، خنثیسازی نهایی و حذف گچ ( ژیپس ) انجام میگیرد.
عامل خنثیسازی در این مرحله سنگآهک و دوغاب سولفات روی قلیایی به همراه ژیپس از مرحله رسوبگذاری سولفات روی قلیایی ( منیزیم زدایی ) است. عناصری مانند آهن، آلومینیوم، آرسنیک، ژرمانیوم و سیلیس باقیمانده در محلول لیچ در این مرحله رسوب میکنند.
بعد از تغلیظ دوغاب تولیدی، سرریز تیکنر ابتدا فیلترشده و سپس به بخش تصفیه ارسال میشود. بخشی از تهریز این تیکنر به مخازن مخصوص حذف آلومینیوم فرستادهشده و دوغاب حاصل، فیلترشده و شستوشو میشود. بخش دیگری از تهریز به مخازن مرحلهدوم خنثیسازی و برجهای خنککننده محلول ارسال می گردد.
-
تصفیه محلول
محلول خام ( PLS ) حاصلشده از مرحله انحلال، محتوی ناخالصیهایی مانند : مس، کبالت، نیکل، کادمیم و کلر است که برای عملیات الکترووینینگ مضر است. این عناصر در طی سه مرحله زیر از محلول خام حذف میگردند :
مرحله اول : کلرزدایی
مرحله اول تصفیه ( کلرزدایی ) غلظت مجاز کلر در الکترولیت ۲۰۰ میلیگرم در لیتر میباشد. جهت جلوگیری از بالا رفتن غلظت یون کلر در الکترولیت با استفاده از یک واحد جداگانه جهت حذف کلر از محلول سولفات روی، این مرحله از لحاظ میزان عنصر ملر، تحت کنترل مداوم قرار میگیرد. به این صورت که حدود ۱/۳ از محلول خام وارد مرحله کلرزدایی میشود، کلرزدایی در PH برابر ۲/۵ و دمایی در حدود ۵۰ درجه سانتیگراد و توسط روی و کات کبود صورت میگیرد.
مرحله دوم : تصفیه گرم
مرحله دوم تصفیه در این مرحله با استفاده از گرد روی و تری اکسید آرسنیک، مس، کبالت و نیکل ترسیب میشوند جهت ایجاد شرایط مطلوب برای رسوبگذاری کامل Cu3As ، CoAs و NiAs از مقادیر معینی سولفات مس استفاده می شود. دمای این مرحله بین ۷۰-۸۰ درجه سانتیگراد در PH=4.5 درنظر گرفتهمیشود. بعد از فیلترکردن، رسوبات مس، کبالت و نیکل با آب شستوشوشده و جهت عملآوری بیشتر یا فروش، در انبار ذخیره میگردد.
مرحله سوم : تصفیه سرد
در این مرحله با افزودن گرد روی، در دمای حدود ۵۰ درجه سانتیگراد و تنظیم PH توسط الکترولیت برگشتی از مرحله الکترووینینگ (PH=4 )، کادمیم به صورت اسفنجی رسوب مینمایند بعد از فیلترکردن، کادمیم اسفنجی به فرآیند تولید شمش کادمیم و محلول فیلترشده آن به مرحله الکترووینیگ ارسال میگردد. کربنات استرانسیوم یا باریم جهت رسوبگذاری سرب به الکترولیت، در چرخه فزوده میشود. ورقهکنی از کاتدهای آلومینیومی بعد از طی مدت زمان معینی به طور مکانیکی صورت میگیرد.
واحد ذوب و ریختهگری
ورقههای روی تولیدشده در واحد الکترووینینگ نخست بر روی یک سکوی ذخیره انبار میشوند تا به طور طبیعی توسط هوا خنک شوند. ورقهای خشکشده توسط یک باسکول وزنشده و به وسیله لیفتراک به کوره القایی تغذیه میشود. در این قسمت کلرید آمونیوم برای کاهش تولید سرباره فلزی اضافه میشود تا از اتلاف فلز روی جلوگیری شود. فلز روی مذاب توسط یک پمپ ویژه از طریق یک ناودان به ماشین ریختهگری شمش منتقل میشود. شمشها بر روی همچیده شده، وزن و بستهبندی میشوند و توسط لیفتراک به انبار محصول حمل میگردند.
تفاوت عمده روش استخراج انحلالی ( Solvent Extraction ) و روش مرسوم در بخش تصفیه است. به طوریکه در روش استخراج انحلالی، روی حلشده در محلول لیچ به طور انتخابی از سایر ناخالصیها جدا میشود، در حالیکه در روش مرسوم، ناخالصیها از محلول لیچ جداشده و محلول خالص سولفات روی استحصال میگردد. بنابراین بخش های آمادهسازی (خردایش، یکنواختسازی و آسیاب)، لیچ، الکترووینینگ، ذوب و ریختهگری و … در هر دو روش مشابه میباشند.
مقایسه روشهای پیرومتالورژیکی با روشهای هیدرومتالورژیکی تولید روی :
- روش پیرومتالورژی در ظرفیتهای تولید بالا مقرون به صرفه نیست ولی روش هیدرومتالورژی در ظرفیت های تولید بالا نیز کاملا اقتصادی میباشند.
- روشهای هیدرومتالورژی برای کانههای با عیار پایین نیز استفاده میشوند اما در روشهای پیرومتالورژیکی فقط کانههای با عیار بالا قابل استفاده میباشند.
- روشهای پیرومتالورژیکی به تغییر ترکیب شیمیایی مواد اولیه حساس هستند به طوریکه اگر میزان برخی از ناخالصیها از حدی بیشتر شود، تولید متوقفشده یا راندمان کاری فرایند به شدت افت می کند.
- مصرف انرژی در فرایندهای پیرومتالورژیکی معمولا بالاتر است.
- با توجه به عدم ایجاد پساب در فرایندهای پیرومتالورژیکی و قابلیت مصرف دوباره پسمانده های حاصل در این روشها، مسائل زیست محیطی در روشهای پیرومتالورژیکی کمتر میباشد.
مقایسه روش مرسوم ( Conventional ) با روش استخراج انحلالی یا SX ( Solvent Extraction )
- روش SX انعطافپذیری زیادی در برابر تغییر ترکیب شیمیایی مواد اولیه روی دارد، به طوریکه استفاده از مادهاولیه روی حاوی ناخالصیهای زیاد، تاثیری بر عملکرد سیستم ندارد. اما در روش مرسوم، فرایند بر اساس میزان ناخالصی ها تا حدودی تغییر میکند.
- کیفیت بالای الکترولیت در روش SX منجر به استفاده از ولتاژ کمتر برق در سلولها شده که در نتیجه باعث مصرف کمتر انرژی برق می شود.
- سطح فلوئور و کلریدها در فضای بخش ( EW ) در روش SX خیلی پایینتر از روش مرسوم است، بنابراین محیط بخش EW عاری از گازهای کلر بوده و در نتیجه باعث جلوگیری از خوردگی ساختمان ها، تجهیزات و مخازن میشود.
- هزینه احداث کارخانه با روش SX ، بیشتر از روش مرسوم است.
- روش SX موفقیت بیشتری نسبت به روش مرسوم در حصول کیفیت SHG داشته است.
بدین ترتیب باوجود اینکه روش SX برتریهای قابل توجهی در مجموع نسبت به روش مرسوم دارد اما سرمایه گذاری اولیه مورد نیاز آن در مقایسه با روش مرسوم بیشتر است. به دلیل وجود واحدهای فعال متعدد و وجود دانش فنی روش مرسوم در کشور، این روش ( با در نظر گرفتن کلیه جوانب امر )، معمولا انتخاب اول واحدهای تولید روی در ایران است.
جدول ۹ ) میزان مواد اولیه مورد نیاز برای تولید یک تن شمش روی
کاربردهای فلز روی
سالانه حدود ۱۲ میلیون تن روی در جهان تولید میشود. بیش از نصف این مقدار درصنعت گالوانیزاسیون مصرف میشود. حدود ۱۴ درصد در آلیاژهایی با پایه روی که بیشتر در صنایع ریختهگری ( Die Casting ) مورد استفاده قرار میگیرد و ۱۰ درصد در تولید برنج و برنز مصرف میشود. مقدار قابل توجهی روی هم در rolled zinc که شامل roofing ،gutter،down pipe است مصـرف میشود. مابقی در ترکیباتی همانند اکسید روی و سولفات روی مصرف میشود، عرضهکنندگان دست اول، طیف گستردهای از مصارف روی را پوشش میدهند.
اصلی ترین کاربردهای فلز روی عبارتند از :
- صنایع ساختمانی
- حمل و نقل
- مصارف خوراکی
- لوازم الکتریکی و الکترونیکی
روشهای روی اندودکردن دیگری نیز وجود دارد که مورد استفاده قرار میگیرند. مثل رنگهای غنیشده با روی، روی الکترواستاتیک، روشهای مکانیکی، این روشها تفاوت زیادی با گالوانیزاسیون دارند و ممکناست برای برخی از محیطها مناسب نباشند.
در حال حاضر ۷۵ درصد از روی مصرفی در جهان از محل معادن و خاک معدنی و ۲۵ درصد از محل روی بازیافتی تأمین می شود. مقدار بازیافت همه ساله در حال افزایش است. میزان بازیافت روی کاملاً به میزان جمع آوری محصـولات روی پس از مصــرف بستگی دارد. بیش از ۹۰ درصد این محصولات پس از مصرف جمع آوری می شوند. روی در تمام مراحل تولید و مصرف قابل بازیافت است.
به طور مثال : از ضایعات روی در تولید ورق گالوانیزه گرفته تا ضایعات فرآیندهای تولید و نصب و نیز در پایان عمر مصرفی.
فولاد پوششدادهشده با روی و سایر محصولات حاوی روی به دلیل عمر طولانی پس از گذشت زمان زیادی از تولید، وارد چرخه بازیافت میشوند. دوام محصولات حاوی روی متغـیر بوده و از ۵ تا ۵۰ سال در خودرو و لوازم خانگی تا بیش از ۱۰۰ سال در ورق های گالوانیزه ( شیروانی ) تغییر میکند. چراغ های راهنمایی خیابانی که با پوشش روی هستند می توانند تا بیش از ۴۰ سال کار کنند.
در طول یک قرن گذشته روی طول عمر فولاد را افزایشدادهاست. پوشش روی اقتصادی ترین روش افزایش محافظت از فولاد در برابر خوردگی است که سالانه حدود ۴ درصد سود ناخالص داخلی کشورهای غیر صنعتی را از بین می برد. فولاد گالوانیزه خواصی دارد که توسط هیچ ماده دیگری تأمین نمی شود. علاوه بر خواص اشارهشده، خاصیت الکتروشیمیایی روی موجب استفاده از آن در تولید باتریها شدهاست. از جمله مهمترین و جدیدترین کاربردهای فلز روی و آلیاژهای اصلاحشده آن، استفاده از آن در ساخت وسایل الکترونیکی نظیر تلفنهای همراه، تبلت و سایر موارد اشاره نمود.
مصارف روی
روی در ساخت سيمان، دندانسازی، ساخت كبريت، كف سازی، ظروف سفالين، لوازم لاستيكی، اتومبيل سازی، لوازم آشپزخانه، روکش فولاد ( گالوانيزه کردن )، تهيه آلياژهای برنز و برنج، لحيم کاری، قوطی های خمير دندان، چسب فلز ماشين تحرير، نقره آلمانی و… است.
از اکسيد و سولفور روی به عنوان ماده رنگی سفيد در رنگ سازی و تهيه پلاستيک، از سولفات روی در رنگرزی و ساخت چسب و از کلرور روی در لحيم کاری و جلوگيری از فساد چوب استفاده می شود.
از آندهای روی جهت جلوگيری از خوردگی بدنه كشتی ها، سكوهای حفاری و خطوط لوله زير آب استفاده می شود. چنانچه روی برای ساخت صفحات روی يا برنج به كار رود، اندازه آلومينيوم آن نبايد از ۰۰۵/۰ درصد فراتر رود. مقدار قلع در نوع عيار بالای روی نبايد از ۰/۰۰۱ درصد فراتر باشد. مقدار آلومينيم در نوع PW نبايد از ۰/۰۵ درصد فراتر باشد.
فعاليت شديد الكتروشيميايي، باعث جلوگيری از خوردگی كاتديک در فرآوردههای آهن و فولادی می شود. آميختگی روی با مس و تشكيل آلياژ برنج كه اين آلياژ دارای ويژگی هايی مانند قابليت استفاده در درجه حرارتهای پايين، محافظت در برابر خوردگی و پرداخت زيبا است.
دو عيار ديگر برای فلز روی به منظور مصارف گالوانيزهكردن مورد قبول واقعشدهاست. يكی به نام عيار گالوانيزهكردن پيوسته ( Continious Galvanizing Grade ) كه تا ۳۵% سرب و مقداری آلومينيم دارد و ديگری به نام عيار كنترلشده سرب ( Controlled Lead Grade ) كه كمتر از ۱۸% سرب دارد و به دور از آلومينيم است.
از جمله موارد مهم استفاده روی در صنایع مختلف میتوان به موارد زیر اشاره کرد :
- روی به صورت بخشی از مخازن باتری ها، در قالبهای ريختهگری و صنعت اتومبيلسازی به كار می رود.
- اكسيد روی به عنوان يک رنگدانه سفيد در رنگ آبی ( اقيانوسها ) و انواع نقاشی استفاده می شود.
- كلريد روی به عنوان يک ضد بو ( اسپری بدن ) و به عنوان ماده نگهدارنده چوب استفاده می شود.
- سولفيد روی در رنگدانههای نورتاب برای ساخت عقربههای ساعت و اشياء ديگری كه در تاريكی بدرخشند، استفاده می شود.
- متيل روی [Zn(CH۳)۲] در سنتز مواد آلی استفاده می شود.
- محلولهایی ( لوسيون ) كه از كالامين ساختهمیشوند، مخلوطی از كربناتها و سيليكات های روی Silicate و Zn-hydroxy- Carbo بوده که در درمان جوشهای پوستی كاربرد دارند.
صنايع ساختمانی
روی در كارهای عمرانی و ساختمانی نيز مورد مصرف قرار می گيرد. اگر چه روی دارای مقاومت بالايی است. به دليل مقاومت خزشی بسيار پايين آن برای مدت ها به عنوان مواد ساختمانی استفاده نمی شد. آلياژهای با روی كم با اساس Zn-Ti-Cu كه دارای چكش خواری بسيار خوب و مقاومت خزشی بالاست، از ۴۰ سال قبل توسعه يافته است. اين مواد را می توان جهت توليد صفحات يا ورق های روی، نورد داد. از اين صفحات می توان در توليد وسايل زهكشی سقف و يا در پوشش ساختمان ها استفاده نمود.
آلياژها
روی در دمای بالاتر از دمای اتاق تبلور مجدد می يابد و مقاومت خزشی پايين دارد. بنابراين، اين عنصر تنها به عنوان ماده سازنده هنگام آلياژ كاری مناسب است. عناصر آلياژی، بيشتر Al، Cu، Mg منجر به كوچک شدن دانه ها، تشكيل بلورهای مختلط يا سخت شدگی رسوب شده و بدين طريق خواص مكانيكی فلز توسعه می يابد. روی در تهيه آلياژهای برنج، نقره، نيكل استفاده می شود. روی در قالبهای ريختهگری و صنعت اتومبيلسازی نيز به كار می رود.
گالوانيزه كردن فولاد
فلز روی در گالوانيزه كردن فرآوردههای فولادی به كار می رود و باعث جلوگيری از خوردگی فولاد می شود. بخش بزرگ اين فرآوردهها در گالوانيزه كردن فولاد، ورقهای پوشش بام ها، مخازن ذخيره، حصار کاربرد دارد.
ورقهای گالوانيزه به صورت كانالهای هوا در سيستمهای تهويه مطبوع و هواكشها و سيستمهای حرارتی نيز كاربرد دارند.
پوشش روی از طريق مكانيسم زير فولاد را در مقابل خوردگی توسط هوا محافظت می كند :
- اثر دی اكسيد كربن و رطوبت هوا بر روی، تشكيل پوشش محافظ با اساس كربنات روی است كه منجر به كاهش سرعت خوردگی می شود.
- به دليل ويژگی الكتروشيميايی حفاظت كاتدی، روی به طور فعال از خوردگی در محلهای آسيب كوچک، قسمتهايی كه پوشش آسيبديده و لبههای صفحات بريدهشده جلوگيری میكند.
- استفاده بهينه از منابع مواد خام جهان ايجاب می كند كه فلزات را از خورده شدن محافظت كنيم. همانگونه كه اتمسفر خورنده تر می شود، استانداردهای حفاظت در مقابل خوردگی نيز، به خصوص در توليد فولاد، بايستی افزايش يابد. در كشورهای صنعتی تقريباً ۵۰ درصد روی جهت جلوگيری از خوردگی استفاده می شود.
روی تجاری (% ۵/۹۹ – ۵/۹۸) جهت گالوانيزه كردن گرم – عميق در تجهيزات توليد و توزيع و روی با درجه خلوص بالا (% ۹۵/۹۹) جهت گالوانيزه كردن پيوسته فنرها و سيم های فولادی كاربرد دارد. فرايند متالوژيكي كه جهت توليد روی با درجه خلوص پايين تر استفاده می شود، كاربرد سرب به عنوان ناخالصی اصلی است. حضور ۱ درصد سرب در مقايسه با محصولات خالص تر، ۴۰ درصد تنش سطحی را كاهش می دهد. هنگام غوطه ور سازی در حمام روی كه تنها چند دقيقه طول می كشد، فلز ۴۵۰۰ درجه سانتیگراد گرم می شود.
فرايند انتشار منجربه تشكيل لايهای از آلياژ آهن-روی بر سطح فولاد شده كه اين لايه چسبندگی پوشش روی را افزايشمیدهد. علاوه بر فرايندهای گرم – عميق، فرايندهای گالوانيزه كردن ديگری نيز توسعه يافته است. در روی اندود كردن الكترولينيک، يک جريان متناوب منجر به نهشت پوشش درخشان ۲۵- ۵ سانتی متری از الكتروليت های اسيدی، سيانيدی يا الكتروليدهای آسكالن بدون سيانيد بر سطح می گردد. البته اين پوشش تنها در مقابل خوردگی های سطح متوسط از فلز حفاظت می كند.
به دليل نسبت بالای روی در پتانسيل اكسيداسيون و احيا از اين فلز برای حفاظت آهن و فولاد در برابر خوردگی استفاده می شود. فلز روی توليد شده از سنگ معدن را روی اوليه ( Primary Zinc ) يا دست اول می نامند. فلز روی حاصل از باطلهها، پس ماندهها و قراضهها را بر حسب نوع فرآيند بازيابی به نامهای ثانويه يا دست دوم ( Secondary )، تقطير دوباره ( Redistilled ) يا ذوب دوباره ( Re-melt ) می نامند. روی اوليه به دو دسته روی الكتروليتی و روی تقطير شده، بر حسب روش احيا به كار برده شده، طبقه بندی می شود.
الکترونيک
فلز روی در سيمهای برقی، مخابرات و پيچ و مهرهها بهكار میرود. اكسيد روی بهصورت ورق در بدنه باطریهای خشک، پوشش سقف صفحههای گراور عكاسی، برای محافظت بدنه كشتی، خطوط لوله و تأسيسات حفاری در دريا بهكار میرود. علاوهبر آن، برای آبكاری پيچ و مهرهها و قطعات فلزی كوچک، تهنشينساختن فلزات نادر موجود در يک محلول، نقرهزدايی سرب به وسيله فرايند Parkes، جداسازی ناخالصیهايی از قبيل مس، كادميوم و نيكل از يک محلول ( قبل از انجام الكتروليز ) از غبار روی استفاده میشود. فريتهای روی ( Zinc Ferrite ) در قطعات الكترونيكی موجود در ترانسفورماتورها ( بوبينها )، آمپلی فايرها، موتورها، تيونرها و همچنين در قطعات الكترونيكی موجود در راديو و تلويزيون و كامپيوتر به كار گرفته می شود.
فريتهای روی ( Zinc Ferrite ) در قطعات الكترونيكی موجود در ترانسفورماتورها ( بوبينها )، آمپلی فايرها، موتورها، تيونرها و همچنين در قطعات الكترونيكی موجود در راديو و تلويزيون و كامپيوتر به كار گرفته می شود.
رنگ سازی
اكسيد روی به دليل دارا بودن خاصيت پوششی اپاسيتی ( Opacity ) در برابر اشعه ماوراء بنفش و ضريب شكست بالا ( High Refractive Index )، در صنايع رنگسازی استفاده می شود كه باعث افزايش پايداری رنگ است.
لاستيک سازی
اكسيد روی همچنين به عنوان فعال كننده و شتاب دهنده اصلی در صنعت محكم سازی لاستيک با گوگرد به كار برده می شود. ليتوپون ( Lito Pone ) كه يک پيگمنت سولفات باريم – سولفيد روی است در صنايع رنگ، لاستيک و مركب چاپ كاربرد دارد.
داروسازی
اسميت زونيت در مصارف دارويی با نام قديم کالامين شناخته می شود و ماده مورد مصرف در صنعت داروسازی، اکسيد روی ZnO حاصل از اسميت زونيت است که درجه خلوص آن بايد بيش از ۹۸ % باشد. اين ماده به صورت پودر صورتی کم رنگ در آب نامحلول بوده ولی در اسيدهای معدنی به خوبی حل می شود.
کالامين اثر ضدخارشی داشته و آن را جهت مصارف خارجی (پوستی) و به شکل پودر، كرمهای ضدآفتاب (لوسيونها) با نام های تجاری معرفی می شوند :
- Aqueous Calamine Cream
- Oily Calamine Lotion
- Calamine Ointment
- Calamine Lotion
کالامين در ترکيبات دارويی به نام کالاموکس که در آمريکا تهيه می شود، نيز به کار می رود. داروهای تهيه شده از کالامين برای خشکی پوست، سوختگی های خفيف، اگزما، خراشيدگی و … کاربرد دارد. اكسيد روی در فرآوری تركيبات ديگر روی كه در ساختن فرآوردههايی مانند مركب، رنگمو، مواد افزونی روغن، داروهای ضد قارچ، براق كنندهها و لينوليوم به كار می روند.
ريخته گری تحت فشار با روی
روی ريختهگری شده تحت فشار ( Zinc die-cast ) يكی از كاربردهای اصلی روی بوده كه توسط آلياژهای نوع ZnAl۴Cu و ساير تركيبات وابسته انجام می شود.
برخی از مزيت های روی در ريخته گری تحت فشار عبارتند از :
- سرعت توليد می تواند بسيار گسترده باشد ( ۱۰۰۰- ۶۰ قطعه ) به نسبت اندازه و پيچيدگی قطعات.
- ويسكوزيته زمينه پايين و دماي ذوب كم آلياژها، محصول با كيفيت بالا را تضمين می كند.
- پايين بودن و قابل كنترل بودن انقباض آلياژهای روی، دقت ابعاد را افزايش می دهد.
- سطوح درخشنده يا مات با انواع پوشش ها قابل دست يابی است.
- به علت طيف توليد وسيع، هزينه ها پايين است. محصولات به سبب ويژگی های مكانيكی و فيزيكی خوب دارای دوام بالايی هستند.
- انرژی مورد نياز اين فرايندها پايين است. قريب ۵۰ درصد قطعات ريخته گری شده تحت فشار از جنس روی در صنعت خودرو مصرف می شود.
- روی ريختهگریشده تحت فشار در ساخت در و پنجره، مبلمان، كابينت قفل و كليد و شير آلات و اتصالات حمام نيز مصرف زيادی دارد.
صنايع اتومبيل سازی
روی در صنايع اتومبيلسازی از جمله در ساخت شبكهها، دستگيره قفل، اجزاء مكانيكی و برقی، بدنه، اتصالات برقی نيز كاربرد وسيع و گسترده دارد.
صنعت چاپ
در صنعت چاپ ( فتوكپی ) نيز اكسيد روی استفاده می شود. تركيبات روی در ساخت رنگهای ضد خوردگی كاتالسيتهای شيميايی، ماده گدازنده جوشكاری، لولههای كاتدی، صفحههای رادار، و مواد افزودنی ( additive ) در روغنهای روانكننده و گريس نيز به كار برده می شود.
تجهيزات ضد آتش و نگهداری چوب
سولفات روی و كلرور روی دو تركيب مهم ديگر هستند كه در تجهيزات ضد آتشسوزی حفظ و نگهداری چوب و مواد گدازنده وجود دارند.
صنايع کشاورزی
در ساخت كود به عنوان يک ماده افزودنی مصرف می شود.
فلز روی ثانویه
فلز روی بازيابی شده به شكل روز افزونی وارد زنجيره عرضه مواد خام می شود. اين توليدات ثانويه از نظر مصرف انرژی بسيار با صرفه بوده و آلودگی كمتری از فرآيند توليد فلز از كنسانتره ايجاد می نمايد. مزايای ذكر شده موجب شده است كه مراكز ذوب فلز نيز به بازيافت روی علاقمند گردند. با وجودی كه علت اصلی اقدام به بازيابی منافع اقتصادی آن می باشد، مسائل زيست محيطی نيز از اهميت خاصی برخوردار است.
در حال حاضر سازندگان در كشورهای توسعه يافته مجبور هستند حتی قبل از طراحی و ساخت يک محصول، سرنوشت آن را پس از اتمام طول عمر مفيد در نظر بگيرند. محدوديت اماكن دفن زباله و نگرانی در مورد دفن مواد خطر آفرين به اين مسائل دامن می زند. شركت معاملات روی آمريكا كه يک شركت بازيابی می باشد تخمين می زند حدود ۱۰ ميليون تن فلز روی كه سالانه در جهان مصرف می شود ۷۰ درصد از سنگ معدن و ۳۰ درصد از بازيابی مواد زائد حاصل می شود. بیش از نیمی از سرب و رویی که امروزه مورد استفاده قرار میگیرد بازیافتی می باشد، که شما می توانید با مطالعه مقاله ” بازیافت فلز روی و مزایای آن ” اطلاعات بیشتری در این زمینه به دست بیاورید.
مصارف روی در ایران و جهان
چشمانداز ترسيم شده توسط گروه مطالعات بينالمللی سرب و روی در خصوص روی اين است كه مصرف جهانی فلز روي با ۸/۴ درصد رشد به ۳۴/۱۰ ميليون تن در دو سال آینده و با ۳/۴ درصد رشد به ۷۸/۱۰ ميليون تن طی بازه زمانی ۲۰۱۸-۲۰۱۴ افزايش يابد. عامل اصلی اين امر افزايش مصرف در صنايع گالوانيزه در چين و سرمايهگذاری در پروژههای زيرساختی مانند ساخت جادههای جديد، خطوط راهآهن و تاسيسات انتقال نيرو، توسعه سريع خانهسازی و صنعت خودروسازی است.
به دليل دسترسی آسان به مواد اوليه ( شمش روی ) برای صنايع مصرفكننده در ایران، خصوصاً در زمينه صنايع گالوانيزاسيون و توليد اكسيد، مصرف آن افزايش چشمگيری داشته به طوری كه براساس اطلاعات حاصله مصرف داخلی در سال جاری به حدود ۷۰ هزار تن رسيده است.
بيشترين ميزان مصرف ظاهری در طی اين سالها (۲۰۱۴-۲۰۱۰) به ميزان ۱۳ ميليون تن می باشد. مصرف ظاهری سرب و روی در جهان طی سالهای ۲۰۱۰ و ۲۰۱۱ دارای مقدار نسبتا ثابتی بوده است و با توجه به ميزان توليد ثابت جهانی در همين سال ها، می توان گفت تعادل نسبی بين عرضه و تقاضا ايجاد گرديده است.
عوامل مؤثر بر قیمت روی
عوامل مؤثر بر قیمت روی را میتوان به پنج دسته تقسیم کرد: ۱) قیمت مواد اولیه، ۲) سطح موجودی انبار، ۳) چشمانداز عرضه جهانی، ۴) چشمانداز تقاضای جهانی و ۵) چشمانداز اقتصاد جهانی. پیشبینی توازن عرضه و تقاضای روی در نمودار ۷ نشان داده شده است.
در نمودار ۸، یکی از عوامل اثرگذار بر قیمت روی، یعنی میزان رشد اقتصاد جهانی نشان داده شده است. این رشد در سال ۲۰۲۰ بهواسطهی همهگیری کرونا، پس از مدتها منفی شد و پیشبینی میشود در انتهای سال ۲۰۲۲، شاهد رشد مثبت ۴ درصدی در اقتصاد جهانی باشیم.
سطح موجودی انبارها یکی دیگر از عوامل اثرگذار بر قیمت روی میباشد. در نمودار ۹، رابطهی بین سطح موجودی انبار و قیمت روی نشان داده شده است.
بر اساس عوامل فوق، پیشبینی قیمت روی طبق گزارشهای دو نهاد معتبر بانک جهانی و انجمن سرب و روی، بهصورت زیر است.
از دیگر محرکهای قیمت روی میتوان به پول ارزان بانکهای مرکزی و بسته اقتصادی حدوداً ۱/۹ تریلیون دلاری، کاهش عرضه و تعطیلی بسیاری از معادن در یک سال اخیر، امید به رشد اقتصادی بعد از کرونا، تداوم رشد تولیدات صنعتی بیشتر و مصرف انرژی و مواد اولیه به همان میزان اشاره کرد. دستاندازهای قیمت نیز مواردی همچون اختلاف بین بهای تمامشده و نرخهای فروش تولیدکنندگان، حساسیت دولتها و بانکهای مرکزی نسبت به رشد قیمتها و افت شدید قیمت بعد از دورههای رشد هستند.
نگاهی به وضعیت تولید و تقاضا در ایران
در ایران، ۱۹۵ معدن فلزی وجود دارند که ۴۳ عدد از این معادن، مربوط به استخراج سرب و روی هستند. از این تعداد، ۲۱ معدن فعال، ۱۵ معدن غیرفعال و ۷ معدن در حال تجهیز میباشند. مهمترین کمربندهای سرب و روی ایران در زنجان، یزد، گلپایگان، طبس، نایبند، انارک و آذربایجان قرار دارند.
ایران بعد از چین، قزاقستان و هند، جایگاه چهارم تولید روی در آسیا را دارد. ۳ درصد از ذخایر جهانی سرب و روی (در حدود ۱۲ میلیون تن) در ایران قرار گرفته و این کشور با تولید ۲/۱۲ درصد از روی جهان، رتبهی پانزدهم تولید را به نام خود ثبت کرده است. ظرفیت اسمی تولید شمش روی ۴۵۰ هزار تن است که در حالت عملی این رقم به ۲۰۰ هزار تن میرسد.
از بین معادن موجود در کشور، انگوران مهمترین معدن کشور است و پیشبینی میشود پس از اتمام ذخایر و قابلیت استحصال از این معدن، معدن مهدیآباد جایگزین آن شود، اگرچه ذخایر این معدن عیار مناسبی ندارد. در شکل زیر، معادن مهم کشور به همراه جزئیات آنها نشان داده شده است.
از میزان محصول تولیدی کشور، بهاندازه نیاز داخلی مصرف و مابقی صادر میشود. قیمتگذاری محصولات داخلی بر مبنای نرخ جهانی روی در بورس فلزات لندن (LME) بوده و در بورس کالای ایران انجام میشود. قیمت صادراتی نیز بر اساس نرخهای LME و با در نظر گرفتن تخفیفات تعیین میشود. در نمودار زیر، مقدار صادرات شمش روی در سالهای اخیر نشان داده شده است.
همچنین ارزش صادرات و واردات محصولات روی ایران بهشرح نمودار زیر میباشد.
چه عواملی بر پیش بینی های قیمت روی اثر می گذارند؟
به طور کلی با وجود انتظار برای افزایش قیمت فلز روی ، نمی شود انتظار داشت که قیمت ها پرواز کنند. چین پتانسیل بالایی دارد تا در صورتی که قیمت فلز روی جهش زیادی داشته باشد، فعال شود. اگرچه داده ها نشان دهنده افزایش قیمت روی می باشد، اما عوامل بسیاری به شرح زیر بر این پیش بینی ها اثرگذار هستند که برخی از آن ها می توانند منجر به افزایش قیمت و برخی دیگر می توانند باعث کاهش قیمت شوند.
برخی از این علل به شرح زیر می باشد :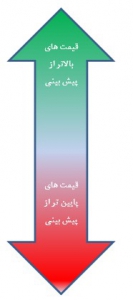
- تاخیر در توسعه معدن جدید
- تولید روی کارخانه های ذوب در چین افزایش پیدا نکند
- مصرف سرانه روی چین همانند ژاپن ، کره جنوبی و تایوان ادامه یابد
- افزایش شتاب مصرف روی به عنوان ریز خوراک در کودهای کشاورزی
- افزایش شدید در استفاده از ورقه های گالوانیزه شده در صنعت خودرو سازی
- جایگزینی ورقه های گالوانیزه با سایر مواد در صنعت خودرو سازی
- آزادسازی غیرقابل کنترل موجودی کالا
- افزایش شدید در عرضه روی از سوی معادن چین
- توازن نامنظم در اقتصاد چین
- احیا تولید روی کارخانه های ذوب در چین
مواد اولیه مورد نیاز جهت تولید شمش روی
ماده اولیه اصلی جهت تولید شمش روی ، سنگ معدن روی به شکل سولفاته یا کربناته می باشد اما مواد اولیه فرعی دیگری نیز برای فرآوری سنگ معدن سولفور روی به کار می رود که در زیر به آن ها اشاره کرده ایم.
- سود سوز آور
- هیدروکسید سدیم
- آب آهک
- اسید سولفوریک
- سیلیس و …
برای اطلاع از آخرین قیمت شمش روی در بازار ایران و خرید آن وارد شوید.
فلوچارت فرآیند تولید شمش روی و شمش سرب
ماشین آلات و تجهیزات فرآوری سنگ معدن سولفور روی جهت تولید شمش روی
- خط فلوتاسیون
- فیدر تغذیه ویبراتوری
- خردکن های jaw
- خردکن های هیدرولیک
- صفحه ویبراتور
- بین های ذخیره
- فیدرهای پندالیوم
- آسیاب Ball
- کلسیفایر اسپیرال
- مخازن همزن دار
- دستگاه فلوتاسیون
- سپراتورهای مغناطیسی
- میکسرهای تیوپی
- خشک کن ها و کانوایرها
- شستشو دهنده های اسپیرال
- تجهیزات الکترولیز
- تجهیزات ریخته گری و ذوب
- کوره ذوب فلز
- مخازن ذخیره مواد شیمیایی نظیر اسید سولفوریک و انواع محلول ها
- برج خنک کننده و راکتور تصفیه
- انواع پمپ ها
- قالب های ۲۵-۲۲ کیلویی برای تولید شمش و …
- تجهیزات مربوط به خط تولید اکسیژن به همراه نیتروژن و آرگون
نتیجه گیری
روی هنوز به وفور در پوسته زمین وجود دارد و ذخایر روی درحالرشد است، اکتشافها ادامهدارد و معادن و پروژه های کارخانه ذوبآهن همچنان در حال آمدن بر روی مدار تولید هستند. اما نکته ای که وجود دارد با قیمت فعلی روی ، بازده پروژه های معدنی و کارخانه های ذوب پایین است. بنابراین هنگامی که قیمت روی افزایش پیدا کند، تامین مالی این سرمایه گذاری ها به علت بازده بهتر، آسان تر خواهد شد. اما امکان دارد تکمیل آن ها چندین سال زمان ببرد.
در این بین، اجماع آرای عمومی وجود دارد که کسری عرضه تا زمانی که معادن و کارخانه های ذوب جدید وارد مدار تولید شوند، ادامه خواهد داشت. این کسری، استفاده کنندگان را ملزم به انبار کردن روی می کند. از طرفی همانطور که این انبارها کاهش می یابد، قیمت روی احتمال بیشتری دارد که افزایش یابد.
بازار فلزات ایران ارائه کننده انواع فلزات با قیمت مناسب است. جهت خرید روی و خرید زاماک با ما تماس بگیرید
دیدگاهتان را بنویسید